Made Smarter Innovation Challenge:
Resilience Focus Case Studies
Building a stronger, more adaptable manufacturing sector
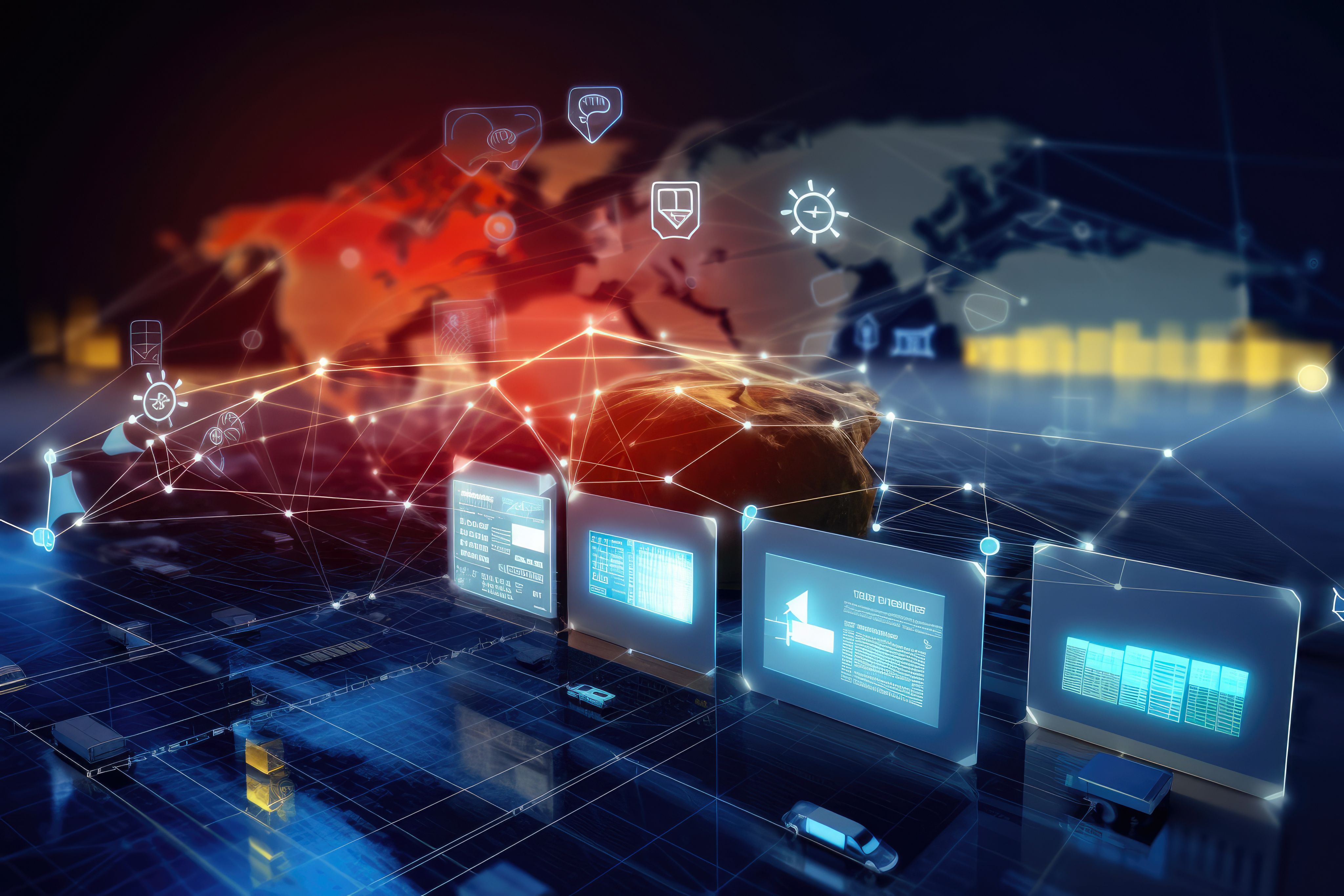
Foreword
The Made Smarter Innovation (MSI) Challenge, delivered by Innovate UK, the Engineering and Physical Sciences Research Council (EPSRC) and the Economic and Social Research Council (ESRC), was launched at a time of significant global disruption, from the COVID-19 pandemic to supply chain shocks and geopolitical tensions. In response, MSI prioritised building resilience in UK manufacturing by equipping businesses with digital solutions that enhance adaptability, security and efficiency. Through targeted investments, the challenge has strengthened supply chains and created more flexible, connected production systems.
MSI has supported initiatives such as the Digital Supply Chain Hub and the International Supply Chain Accelerator, enabling manufacturers to navigate complex challenges with data-driven insights. The £18 million Connected Digital Supply Chains programme has further enhanced collaboration, ensuring companies can better manage disruptions and meet fluctuating demand. Additionally, digital twin technology and blockchain applications have been explored to provide increased transparency and efficiency in industrial operations.
As manufacturers continue to face evolving global pressures, the challenge remains committed to fostering digital resilience. By embedding intelligence and connectivity into supply chains and production environments, MSI is helping businesses future-proof their operations, ensuring the UK maintains a robust and competitive manufacturing sector.
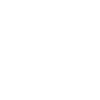
The Digital Spare Parts Supply Chain (DSPSC)
Connecting predictive maintenance software to automated stock management technology could enable factory machines to order their own replacement parts
Could a welding machine order its own replacement for a worn-out part? The Digital Spare Parts Supply Chain (DSPSC) project aimed to answer that question and demonstrate how smart technologies could be used to transform factory maintenance in the future.
With £227,000 of funding from the Made Smarter Innovation Challenge, DPSPC brought together supply chain management company NBT Group Ltd, along with industrial software business Senseye Ltd and Northumbria University to explore how AI could be applied to inventory control and supply chain management in the manufacturing industries.
“At the moment, factories rely on people manually checking machinery [for faults] and ordering parts,” said project lead Toby Bridges, Executive Chair at NBT Group. “Our vision is a smart system that can predict when a part needs to be replaced and then order it – all without the need for human intervention.”
DSPSC investigated the feasibility of connecting two smart technologies to achieve this goal: Senseye Ltd’s predictive maintenance software, which provides industrial maintenance teams with an indication of which parts will need replacing and when; and NBT Group’s stock management software.
“Our vision is a smart system that can predict when a part needs to be replaced and then order it – all without the need for human intervention.”
“For a factory machine to be able to order its replacement part, data must be able to flow accurately through both systems, so we worked with Senseye and Northumbria University’s Global Operations and Supply Chain Competitiveness research interest group to widen our thinking on how to integrate NBT Group’s supply chain technologies into other systems and technologies across a manufacturing plant,” said Bridges. “We also modelled the benefits such a system would bring across various sized factories, which suggested the value of those savings on a large manufacturing site could be in the region of £40 million.”
These potential savings come from multiple efficiencies. Removing administrative and manual tasks, and connecting these systems digitally, means unnecessary stock holdings could be reduced, freeing up space for production, driving down costs and carbon emissions.
It also impacts the workforce, said Bridges. “A connected factory doesn’t need someone to check on machinery twice a day, so it allows businesses to utilise people in higher value roles. With levelling up, there is a lot of discussion about better quality jobs, and this type of technology can open the doors.”
Connecting predictive maintenance and digital supply chain technology could also offer benefits to other sectors. “In this instance, we looked at factory machinery but there is scope for any organisation that has machines and parts that require repair – an ambulance perhaps – or industries that have a digital inventory, such as a finance system,” said Bridges.
“The outcomes and knowledge acquired from this project will pave the way for further research and development, with the ultimate aim of exploiting new technology to help increase productivity, create more highly skilled roles and become more economically, socially and environmentally sustainable.”
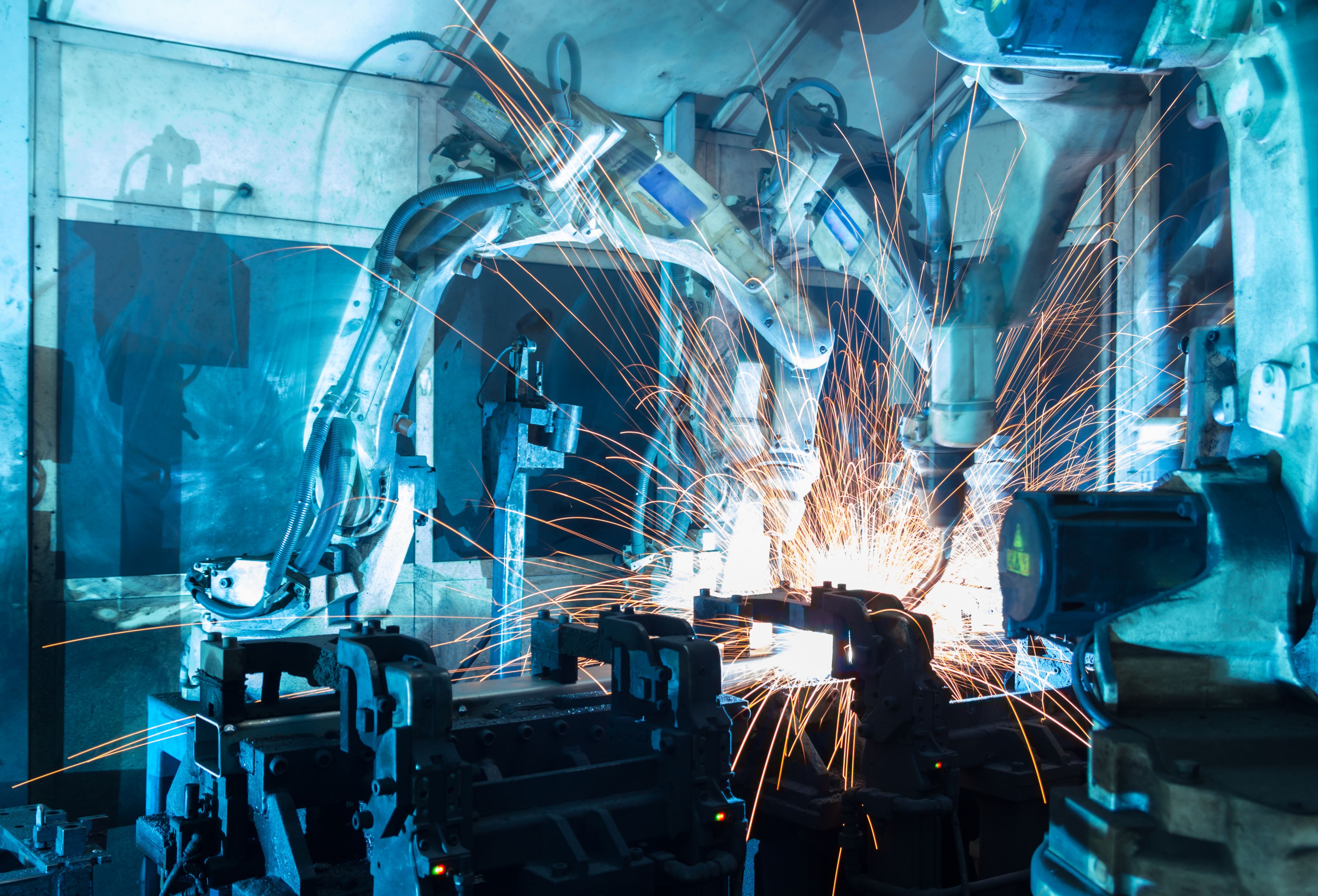
Foods Connected
An interoperable digital platform aims to track and trace food products from farm to fork – helping to improve efficiency, productivity and transparency among food business operators and consumers
Increasingly, consumers want to know where their food comes from, how it’s made and even how it’s farmed. It means there is a growing demand for transparency in food supply chains. However, tracing food data trails along such complex supply chains is a time-consuming process.
“The food industry has become increasingly systemised over the last 20 years, but digitalisation of food traceability information has not progressed at the same pace,” said Dr Stephanie Brooks, Implementation Manager at Foods Connected, which develops software solutions for the agri-food industries. “A lot of information is still inputted manually, which can be prone to error. Where systems are digitised, they often do not connect with each other. So, any traceability exercise involves the labour-intensive task of retrieving data from all those different systems.”
Foods Connected is leading a project to create a digital platform – Trace Connected – that tracks and traces products from farm to fork. Using a centralised cryptographic ledger and internet of things (IoT) technologies, the platform aims to provide real-time information that enables an end-to-end trace to be extracted in seconds instead of hours.
“Trace Connected is like a reservoir of information, pooling all the information from different systems into one place,” said Dr Brooks. “It means any potential compromises within a supply chain can be seen, and more informed, pro-active decisions can be made – potentially saving money and reducing waste, as a result.”
A key aim for the project was to ensure the platform was developed with the food industry in mind. “There’s no point in developing technology that is not practical to use in the real settings of farms and factories. The nature of the food industry, with its many moving parts and tight margins, meant the interoperable platform had to easily integrate with existing systems and be cost-effective,” said Dr Brooks. “The centralised cryptographic ledger, for example, has the same benefits as blockchain in terms of data integrity, but is more affordable.”
“Trace Connected is like a reservoir of information, pooling all the information from different systems into one place.”
Food manufacturing project partners Hilton Foods UK and OSI Food Solutions UK acted as use cases, providing insight and data about current levels of digital maturity, how they collect and track information, and how data can be integrated into one system, which was used to inform the design of Trace Connected.
Planet IoT and Poultry Sense investigated the use of IoT technologies, in cattle and poultry sheds that record environmental and physiological parameters, such as temperature and water intakes. These metrics allow the producer to adjust for efficiency or productivity, and track health data to improve welfare outcomes, which is a key driver in the industry.
The project team are also exploring the potential of incorporating food-safety and quality-based data into the system, as well as exploring general obstacles to widespread adoption of interoperable traceability in the agri-food industry. Combining this extensive data capture with a tamperproof ledger could help ensure product integrity and significantly reduce the potential for food fraud throughout the supply chain.
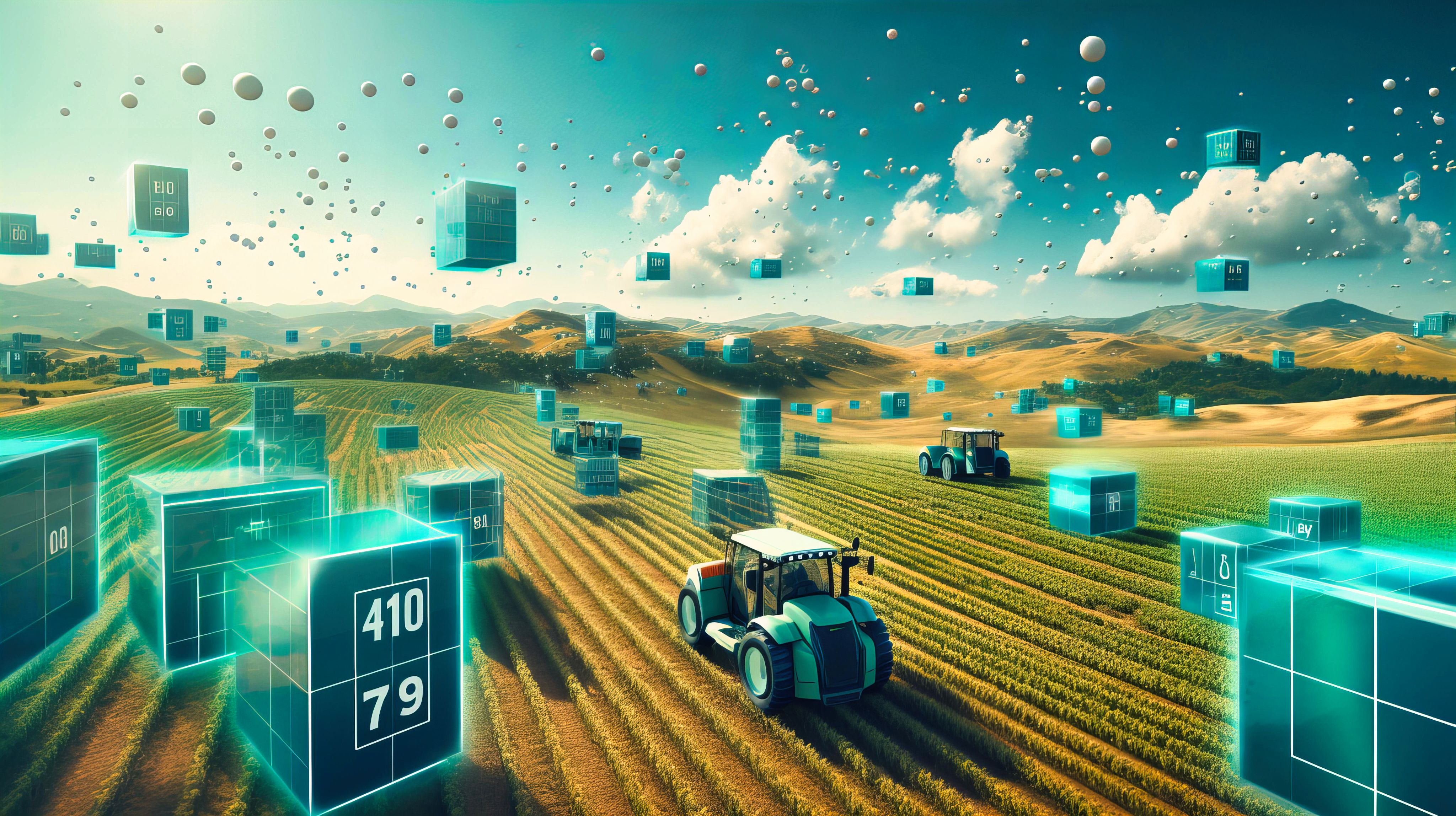
Cranswick & Singular Intelligence
AI solution demonstrates supply chain efficiency potential for FMCG sector
A pioneering AI-driven data analytics solution has demonstrated its potential to transform supply chain efficiency in the fast-moving consumer goods (FMCG) sector. Developed by Singular Intelligence (SI), the technology was trialled in partnership with supermarket chain Sainsbury’s and food producer Cranswick as part of the Made Smarter Innovation Digital Supply Chain Hub (DSCH) programme.
The project focused on mitigating supply-demand imbalances in Sainsbury’s Taste the Difference pork range. By interpreting market signals, the AI solution significantly reduced food waste by up to 70% on some products and improved product availability by up to 5%. Cranswick also benefited, achieving a 15% reduction in oversupply to the retailer.
Following the successful proof of concept, Cranswick is now considering integrating the AI system into its broader digitalisation strategy. Meanwhile, SI has expanded its supply chain team and is working with other FMCG businesses to implement its technology.
"...projects like this from the Digital Supply Chain Hub will help break down existing silos and drive impactful change."
Led by Digital Catapult, the DSCH programme aims to accelerate the adoption of digital technologies within UK supply chains. By leveraging real industry data, this initiative showcases how AI-driven solutions can address major challenges, including sustainability, resilience and operational efficiency.
Cranswick, a major pork producer supplying UK and international markets, has faced significant challenges due to economic uncertainty, global conflict and labour shortages. These disruptions have led to inefficiencies in supply planning, resulting in revenue losses and increased food waste. The company is committed to becoming the world’s most sustainable meat producer by optimising its supply chain through robust data analysis and continuous process improvements.
SI, founded in 2017 and based in London, has been developing its flagship AI-powered forecasting tool, CatmanAI. Having previously worked with Unilever to analyse consumer preferences, the company applied CatmanAI’s abilities to the supply chain sector. The solution incorporated demand-sensing technology to track sales, availability and external factors such as weather. Additionally, supply-sensing technology assessed production risks and supply shocks, generating actionable insights to balance supply and demand effectively.
The implementation of AI yielded substantial benefits. Sainsbury’s saw product availability improve by 2-5% while reducing food waste by 50-70%. Cranswick successfully reduced its pork oversupply by over 15%. These results underscored the AI platform’s ability to enhance efficiency, reduce waste and drive more sustainable operations.
Encouraged by the positive outcomes, SI has expanded its AI team and is now engaging with global FMCG leaders to explore further applications of its technology. Industry-wide, this pilot project highlights the transformative potential of AI in supply chain management. However, for widespread adoption, businesses must overcome challenges related to collaboration and data transparency.
Sarvesh Kumar, CEO, Singular Intelligence, said: “Innovation doesn't exist in isolation. It needs an ecosystem to flourish, one that brings together technology companies like us, customers in need of solutions to their pain points and investors to bring the partners together. I am confident that projects like this from the Digital Supply Chain Hub will help break down existing silos and drive impactful change.”
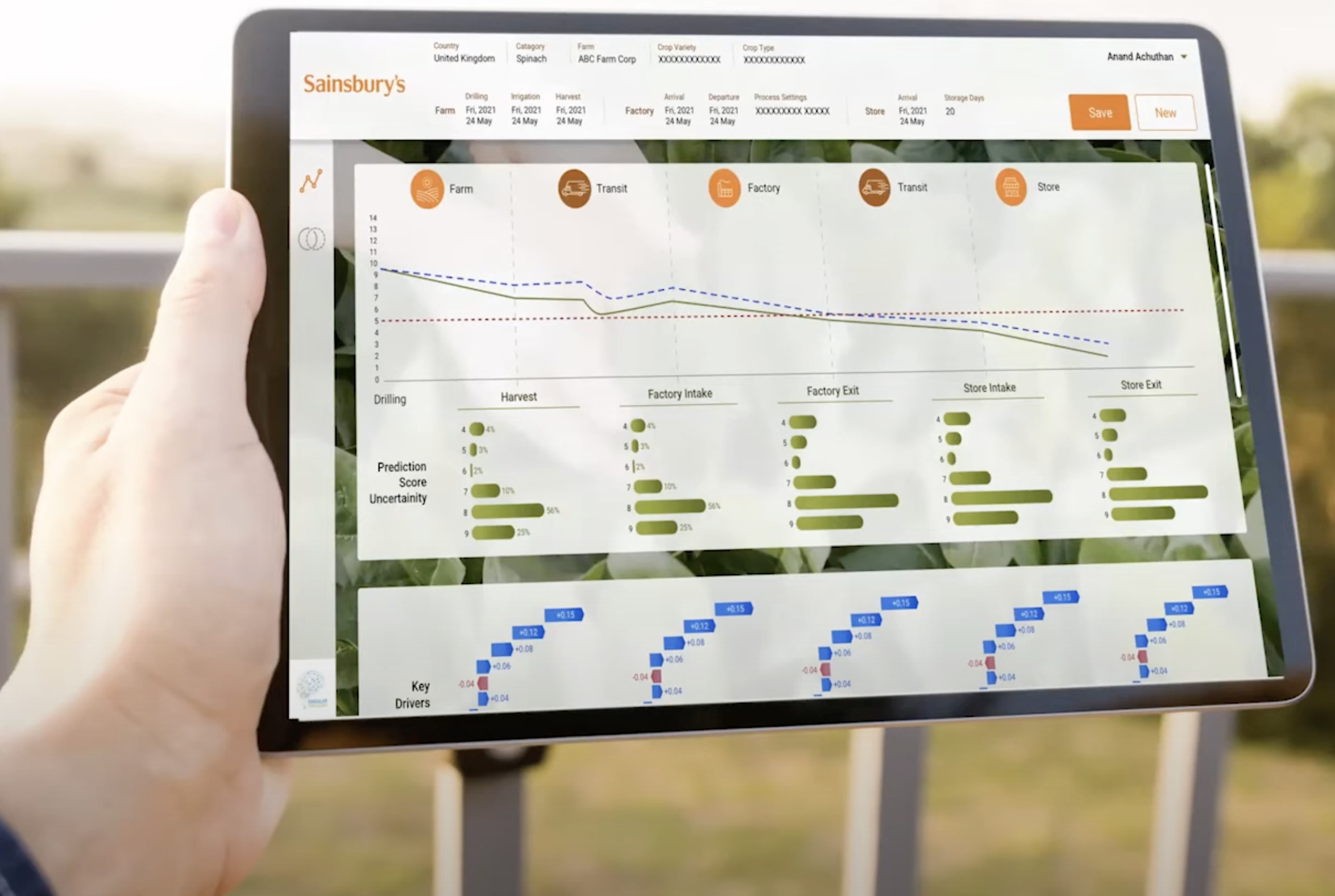
P&G
The ARGUS project investigated how digital technology could be used to test for microbial contamination with funding from the Made Smarter Innovation challenge
Protecting home and personal care products, such as shampoos and washing up liquids, from microbial contamination is a key challenge for manufacturers. A build-up of microbes can create manufacturing problems, requiring cleaning and sanitisation of the equipment, or even pose a risk to consumers, leading to expensive product recalls.
To help ensure only ‘fit for purpose’ products make it to the supermarket shelf, stringent checks are in place, with samples taken at each stage of the supply chain for testing.
“The issue is that the current microbiology-based tests involve a very slow and laborious process – samples can sit in an incubator for up to three days,” said Andrew Dorset, Senior Director for Quality Innovation at consumer goods multinational Procter & Gamble (P&G). “It means a lot of product – and therefore money – is tied up waiting to see whether any microbial contamination has grown on an agar plate or whether it is safe to continue to the next stage of the process.”
With £248,000 of funding from the Made Smarter Innovation Challenge, P&G led the ARGUS project, which investigated how digital technology could be used to test in real time and without stalling the product on its journey through the supply chain. Like the giant in Greek mythology after which it was named, ARGUS has many ‘eyes’ – in this case, the very latest in optical sensor technology from the University of York.
"...there is scope for this to be scaled up further and create a whole new, highly-skilled sector for this technology across a range of industries."
Using the supply chain of the well-known Fairy Liquid brand as a case study, with one of its raw materials suppliers Libra Speciality Chemicals, the project explored how sensors could be deployed at key points to detect the build-up of microbes (biofilm) on surfaces or in flowing liquids. A digital platform prototype was developed to capture the data and provide real-time measurements.
“The technology can pinpoint any problems inline and as they occur, which enables more targeted interventions, whether that’s sanitising or shutting down that particular line,” said project lead Lucia Mendez-Mata, Senior Manager for Corporate Quality Assurance at P&G.
The technology has the potential to create around $1million of direct savings to the UK Fairy Liquid supply chain. Savings come through increased productivity and agility, as well as a reduction in inventory. There are also savings – both economic and environmental – in terms of a more targeted approach to cleaning.
“Currently, equipment is sanitised routinely with hot water. Knowing exactly where and when to clean could save energy and water,” said Mendez-Mata.
Dorset said: “This innovation is very relevant to our fast moving consumer goods liquids businesses, but it has potential application across many other UK supply chains. We are already working on ARGUS II, which takes the proof of concept trials from the feasibility study lab pilots to real factories – but there is scope for this to be scaled up further and create a whole new, highly-skilled sector for this technology across a range of industries.”
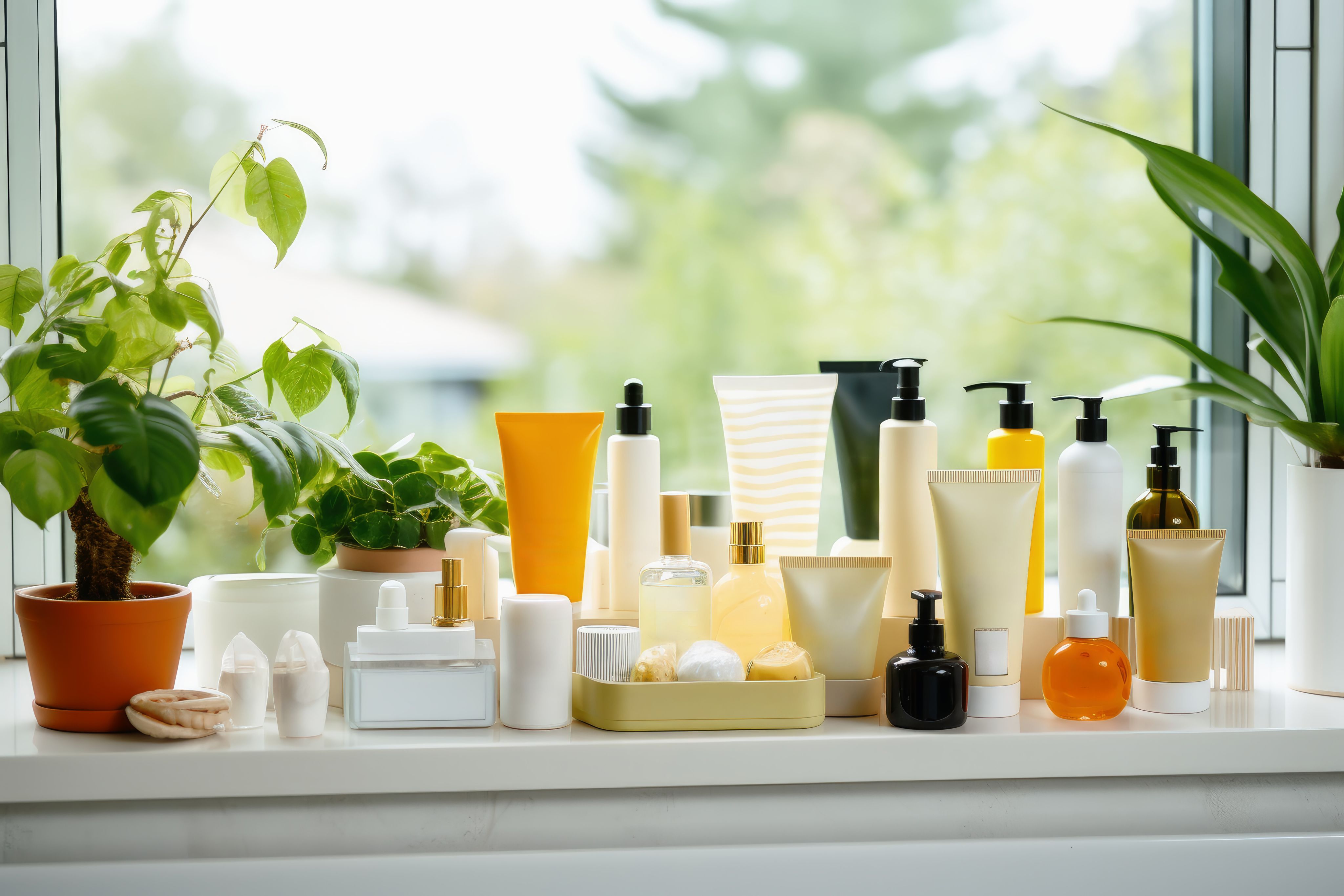
PragmatIC Semiconductor
Empowering the NHS advanced therapies ordering prototype IT system with Manufacturing insight from an electronic batch manufacturing system
A project has developed ‘smart’ labels that could enable recycling centres to sort plastic packaging more efficiently, and even provide consumers with instructions on how and where to recycle their waste. The SORT-IT project explored the feasibility of electronically ‘tagging’ packaging so that it can be identified and tracked.
“Typically, material recovery facilities sort packaging using a near-infrared optical sorting machine. However, the complexity of packaging materials, differences in colour and contamination with food residue mean a large proportion is missed or incorrectly sorted – and a lot of valuable material instead ends up in landfill or incineration,” said Joshua Young, Circular Economy Lead at PragmatIC Semiconductor, which led the project.
PragmatIC Semiconductor innovates and manufactures low-cost, flexible electronics that enable everyday objects to become smart and connected. With £274,000 funding from the Made Smarter Innovation Challenge, the company worked with the University of Sheffield’s Advanced Manufacturing Research Centre (AMRC) to demonstrate how its ultra-low-cost near field communication (NFC) technology could be used to identify, track and sort waste moving along a conveyor belt.
“[The technology] significantly improves the sorting accuracy of mixed recycling, which not only reduces the amount going to landfill, but also means materials are not ‘downcycled’ into lower grade materials.”
Labels using PragmatIC’s NFC technology were applied to items of packaging to provide them with a unique identity. Sensors deployed on a conveyor belt were then able to read the label, identify the packaging, localise its position and remove it for sorting using a robot arm.
“It means the packaging can tell a machine about its material composition, as well as where or how it has been used,” said Bobby Manesh, Head of Research at AMRC Cymru. “It significantly improves the sorting accuracy of mixed recycling, which not only reduces the amount going to landfill, but also means materials are not ‘downcycled’ into lower grade materials.”
This is important because the food and drink packaging industry is struggling to secure enough high-quality material for recycling, known as recyclate, said Young. “There’s growing demand for high quality recyclate, both from industry commitments to plastic targets and from brands and retailers who face a plastic packaging tax at £200 per ton of packaging with less than 30% recycled content.”
Building on the success of the SORT-IT project, PragmatIC Semiconductor and the AMRC are now working on the £1.4 million project TRACE (Technology-enabled Reusable Assets for a Circular Economy), which aims to maximise the recovery and reuse of high value materials through digital technologies.
“We are exploring opportunities for the technology to digitalise reusable systems, enabling them to become a reality at scale. For instance, could consumers return packaging in-store or through online delivery and obtain incentives or rewards for doing so?” said Young. “For environmental and economic reasons, we need to dramatically increase the return and capture of food-grade plastics. This type of engagement could help consumers see plastic as a valuable asset to re-use many times rather than as something to use once and throw away.”
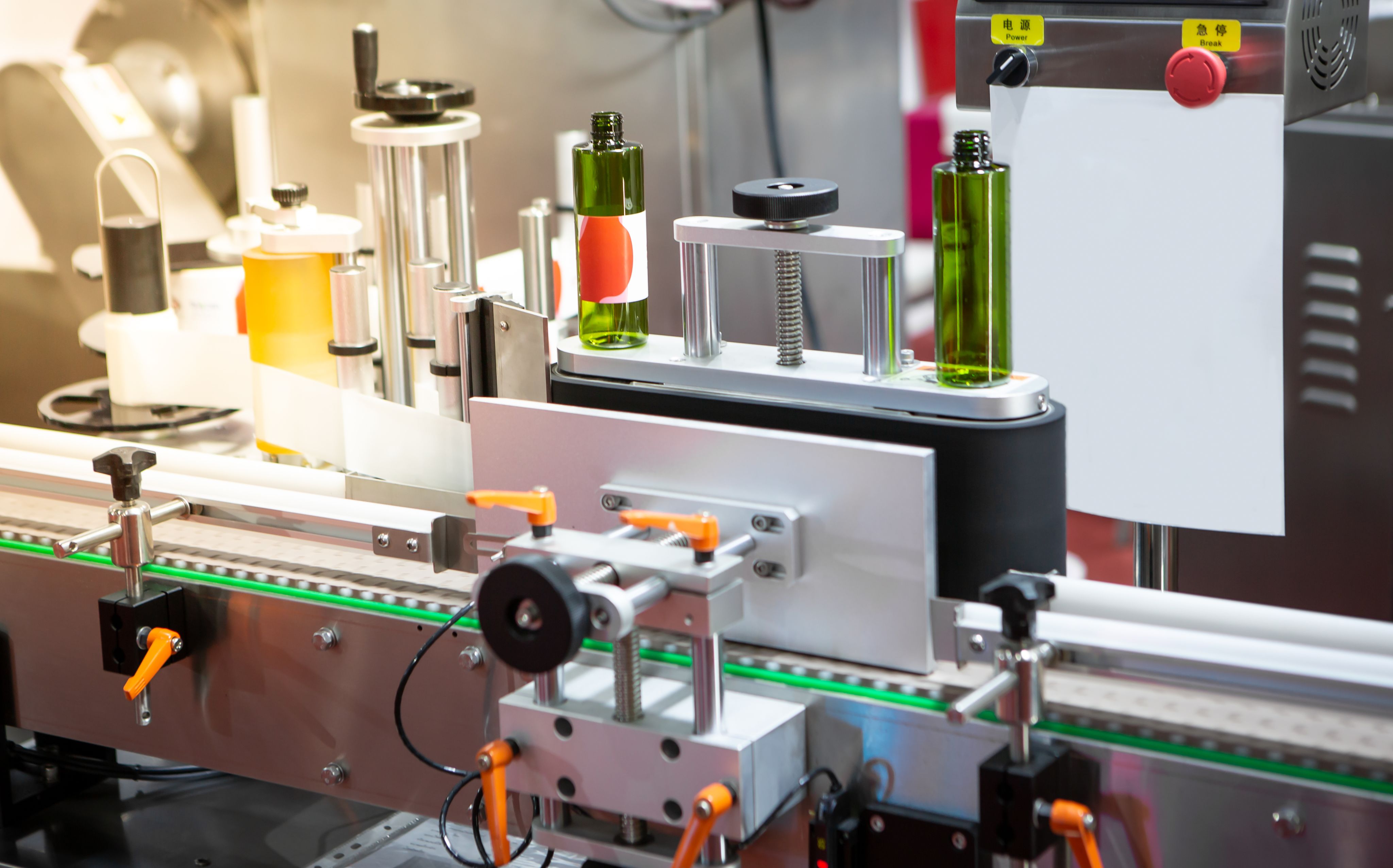