Made Smarter Innovation Challenge:
Productivity Focus Case Studies
Smarter factories, faster processes, greater efficiency
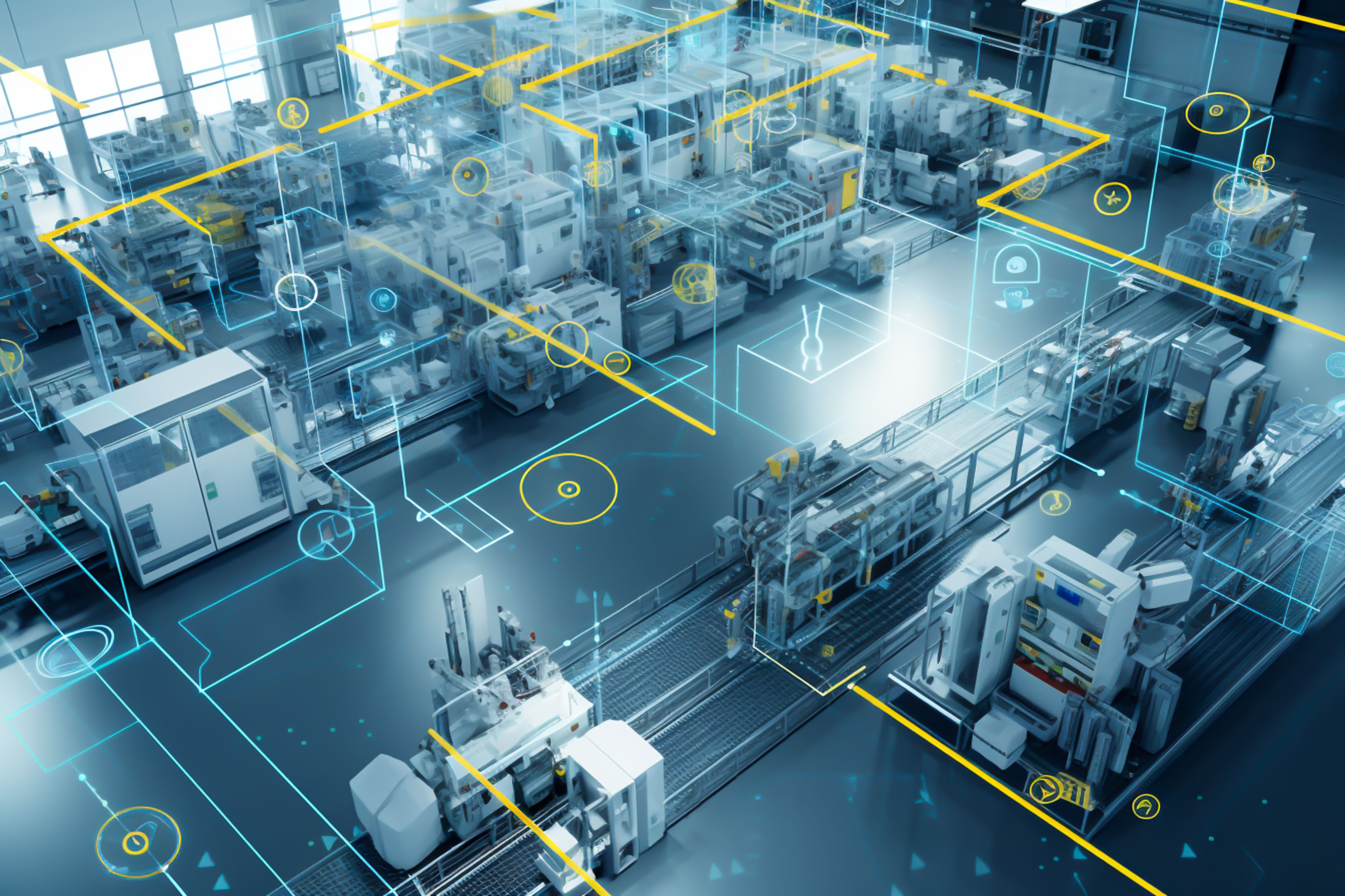
Foreword
Productivity remains at the core of the Made Smarter Innovation (MSI) Challenge, delivered by Innovate UK, the Engineering and Physical Sciences Research Council (EPSRC) and the Economic and Social Research Council (ESRC), driving efficiency through cutting-edge digital transformation. By investing in AI, automation, industrial IoT and data-driven decision-making, MSI has supported UK manufacturers in enhancing output while reducing operational costs. Since its inception, the challenge has enabled businesses to create smarter, more connected production environments that improve efficiency and global competitiveness.
Key initiatives such as the Smart Manufacturing Data Hub and Sustainable Smart Factory funding call have demonstrated how digital technologies can optimise factory operations and streamline processes. With an aim to increase productivity by 30% across the sector, MSI has facilitated the development of new solutions that improve manufacturing speed, precision and agility. By bridging the gap between innovative digital technology providers and manufacturers, the challenge has accelerated the development of game-changing tools.
With over 600 use cases developed and 285 new technologies adopted, the challenge has already delivered measurable impact. The future of UK manufacturing depends on the continued evolution of digitalisation, ensuring companies can achieve greater efficiency, maintain competitiveness and unlock new opportunities for growth in an increasingly complex global market.
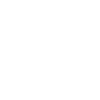
A3L & HAL Robotics
HAL Robotics and A3L develop adaptive self-learning robotic cell for linishing and polishing
A collaborative research and development initiative between A3L, a robotic systems integrator, and HAL Robotics, a human-robot collaboration software specialist, has revolutionised automation in finishing processes. Supported by Made Smarter Innovation, the project has delivered a self-learning robotic cell that adapts to diverse manufacturing requirements, significantly reducing barriers to automation adoption.
The project’s impact could be profound, particularly in sectors where manual finishing operations – such as sanding, polishing and finishing – are labour-intensive, inconsistent and costly. HAL Robotics’ innovative software, decode, has dramatically reduced programming times from up to a week to mere seconds.
This breakthrough enables manufacturers to integrate robotic automation seamlessly, unlocking substantial productivity gains.
Initial implementation within plastics and automotive manufacturing has yielded remarkable efficiency improvements. For example, a process that previously required 10 working days has been reduced to just 12 hours. Similarly, automation in car door polishing has allowed human operators to focus on higher-value tasks while robots handle repetitive and labour-intensive finishing work.
The project introduced three key technological advances:
- Adaptive programming: Operators with no robotics expertise can now influence robotic workflows, significantly lowering technical barriers to adoption
- Smart end effectors: A3L’s adaptable tool adjusts to complex surface geometries, ensuring consistency and quality in finishing processes
- AI-driven process optimisation: Sensor data and digital imaging enhance precision, improving the longevity of consumables and reducing waste.
These innovations have resulted in a scalable, self-programming robotic cell currently undergoing trials with manufacturing partners. The project has demonstrated significant potential for cross-sector applications, including welding, plasma cutting and even food production.
“This project has cemented our relationships with A3L and opened doors to new partnerships, including robot OEMs and potential investors.”
For HAL Robotics, the success of this initiative has led to the launch of decode, a market-ready software solution applicable across multiple industries. It has also facilitated new strategic partnerships with robotic original equipment manufacturers (OEMs) and investors, positioning the company for future growth.
A3L has leveraged its enhanced expertise in robotic finishing to explore new research and development opportunities. The project has accelerated its ambition to become the UK’s leading automation specialist for finishing operations, with aspirations for international expansion.
Beyond immediate industry impact, the R&D process has identified opportunities for further AI-driven optimisation, including improving the lifespan of abrasives and reducing material waste. These developments contribute to the broader goals of sustainability and efficiency in advanced manufacturing.
Sebastian Andraos, co-founder and CEO of HAL Robotics, said: “The Made Smarter Innovation project has been game-changing for our company. We have developed and launched decode, which is being marketed for all finishing processes and adapted for a range of potential industry applications, from welding and plasma cutting to icing cakes and inspection tasks. It has cemented our relationships with A3L and opened doors to new partnerships, including robot OEMs and potential investors.”
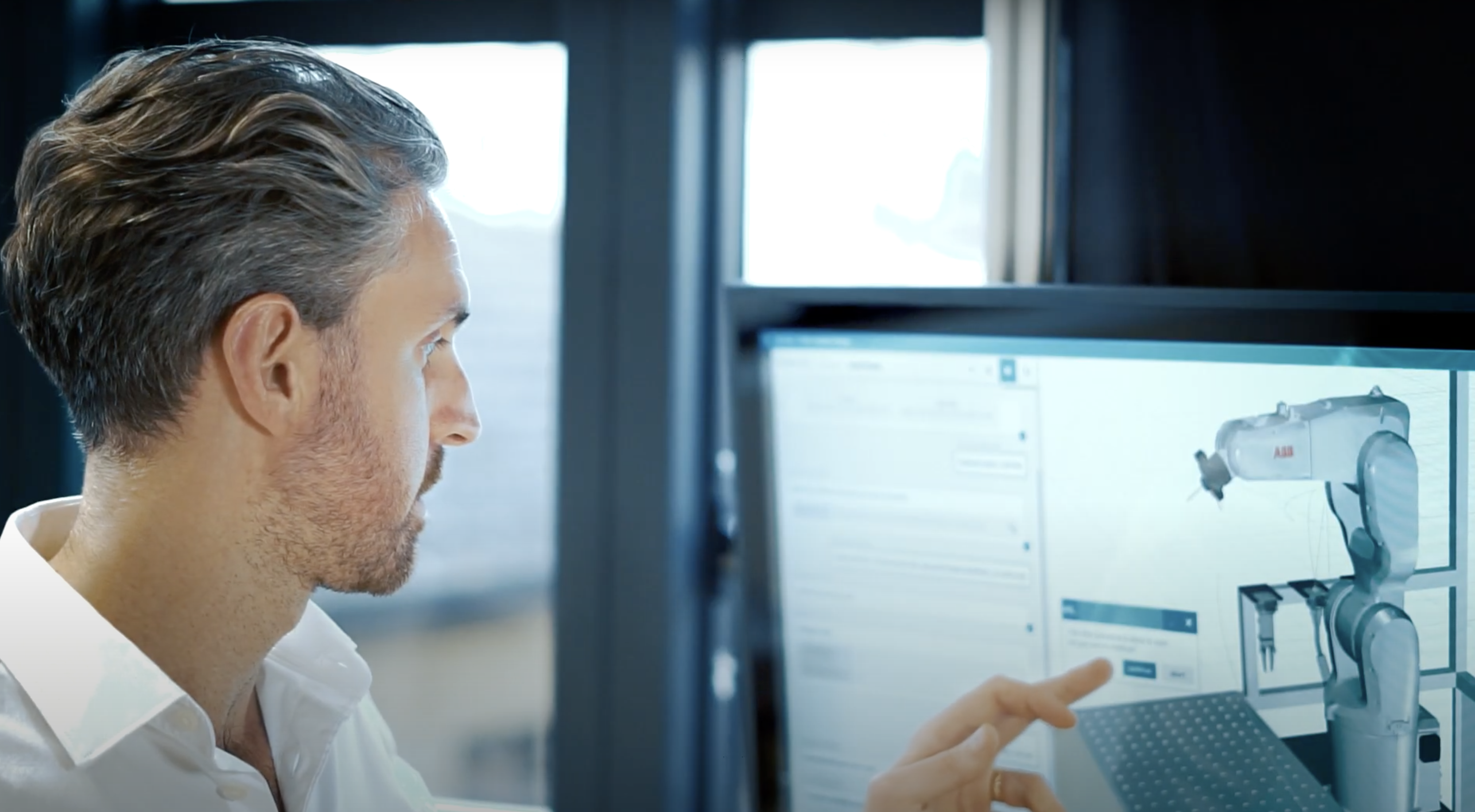
DM2
Collaboration demonstrates how industrial digital technologies makes the development and manufacturing of medicine faster, more efficient and sustainable
A pioneering collaboration led by the Continuous Manufacturing and Advanced Crystallisation (CMAC) centre at the University of Strathclyde is transforming pharmaceutical manufacturing through digital technologies. The Digital Medicines Manufacturing (DM²) initiative, in partnership with Made Smarter Innovation, industry leaders and academia, is accelerating the adoption of industrial digital technologies (IDTs) to enhance efficiency, reduce waste and optimise supply chains.
DM² has introduced cutting-edge innovations such as collaborative robotics, AI and digital twins to enable on-demand, autonomous pharmaceutical manufacturing. These advancements support rapid responses to clinical trial supply demands and personalised medicine production.
One of the standout innovations is the Tableting DataFactory, a breakthrough platform that has reduced pharmaceutical tablet development time from months to less than a day – an efficiency improvement of up to 90%. This AI-driven system not only speeds up production but also cuts material waste by 60% and costs by 50%, contributing to more sustainable and cost-effective manufacturing.
DM² has also advanced digital quality control methods, ensuring pharmaceutical products meet regulatory standards while streamlining traditionally fragmented processes. The ESTAN toolbox, a world-first quality assessment tool, enhances the predictive capabilities of digital twins and optimises process control. Digital simulations for capsule filling have further improved consistency and reliability in production.
The initiative has explored real-world applications of IDTs in healthcare manufacturing supply chains, introducing digital platforms that link patient demand with production capabilities. These tools support adaptive manufacturing networks, enhance resilience in clinical trials and prevent stock shortages, improving overall supply chain efficiency.
“This approach not only accelerates drug development but also reduces costs and waste, while the SkillsFactory initiative helps build a skilled workforce to support these advancements.”
To accelerate industry adoption of these technologies, DM² is launching SkillsFactory, an online training resource set to go live in Spring 2025. This platform will provide flexible, personalised learning opportunities in IDTs, addressing the skills gap in digital pharmaceutical manufacturing. Augmented and mixed reality applications are also being developed to enhance operator decision-making and facilitate real-time remote monitoring.
Prof Alastair Florence, CMAC Director and Principal Investigator on DM2, said: “By integrating data acquisition, automating tablet production and enhancing quality control, DM² creates a more adaptive and resilient supply chain. This collaborative, systems-based approach not only accelerates drug development but also reduces costs and waste, while the SkillsFactory initiative helps build a skilled workforce to support these advancements.”
The impact of DM² has been far-reaching, with 13 first-generation and 23 second-generation demonstrators developed, setting the stage for a fully integrated, data-driven manufacturing ecosystem. The initiative has upskilled around 600 professionals, published over 20 research articles and delivered more than 300 presentations, contributing to the growing expertise in medicines manufacturing in Scotland.
As CMAC continues to expand its research portfolio and drive industry adoption, DM² is laying the foundation for a digitally enabled, more sustainable pharmaceutical sector. The initiative is poised to extend its innovations to other dosage forms such as inhaled and liquid medicines, further revolutionising drug development and manufacturing.
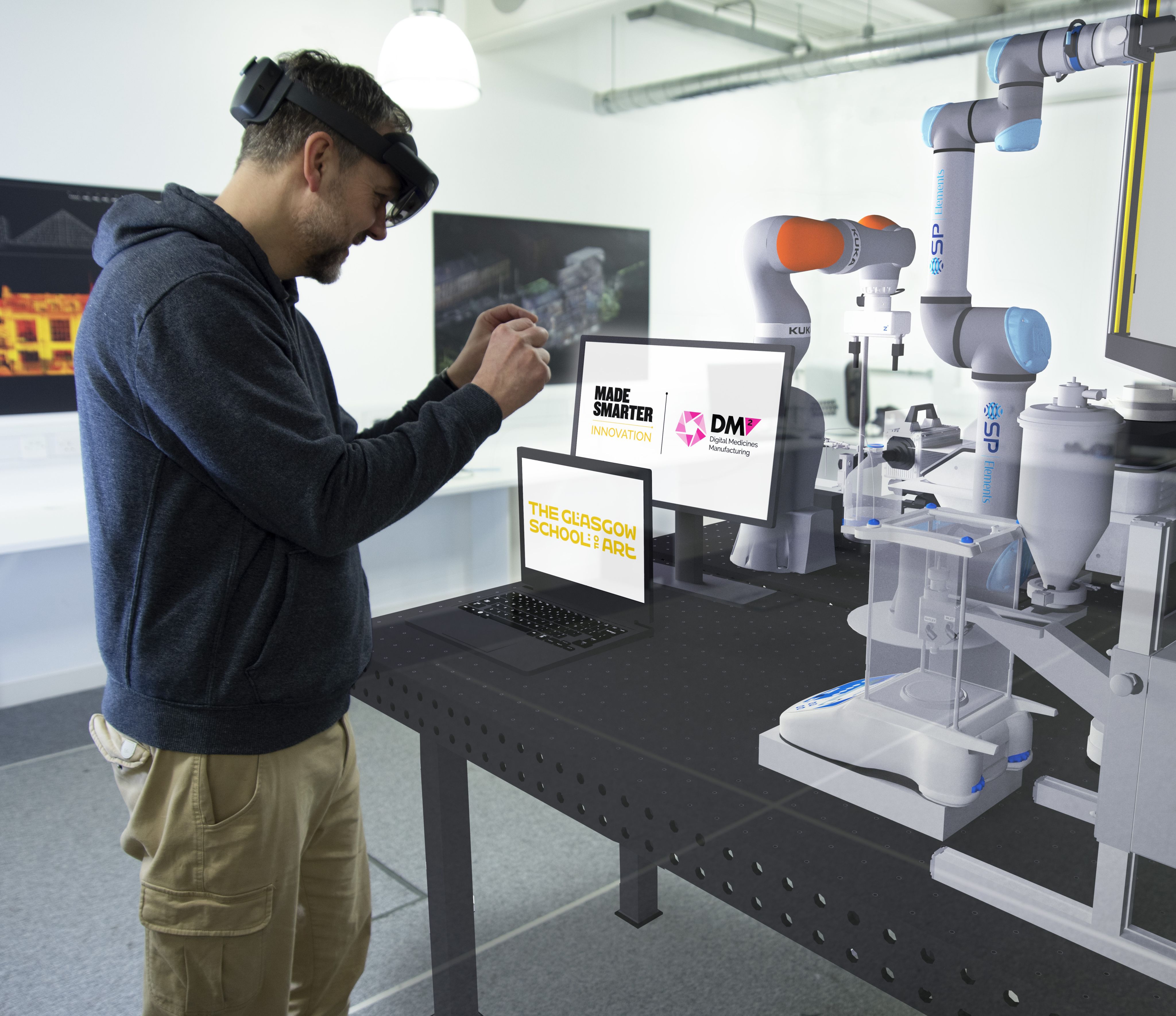
Raplas
A manufacturer of 3D printing technologies has produced a new automated solution that enables components to be made quicker, cheaper and more efficiently
Raplas, a London-based manufacturer of 3D printing technologies, has partnered with FMS, a foundry machinery expert, and Northumbria University to develop a cutting-edge automated solution for the sand-casting industry. This initiative, funded by the Made Smarter Innovation programme, aims to enhance efficiency, reduce costs and enable foundries to produce complex components more rapidly and sustainably.
Sand casting has long been a crucial process in manufacturing, particularly in the automotive and aerospace sectors. However, traditional methods are inefficient, energy-intensive and generate significant waste. The production of moulds requires extensive manual intervention and post-processing, limiting efficiency and flexibility.
While 3D printing presents a promising solution, existing systems are often too large, expensive and difficult to integrate into foundry production lines. Raplas identified an opportunity to create a more accessible and cost-effective additive manufacturing solution tailored to the sand-casting industry.
"Our solution represents a step-change for the foundry industry, making 3D sand printing more accessible and viable."
The company, alongside Northumbria University and FMS, developed a modular 3D printing system designed to seamlessly integrate into foundries of all sizes. Key innovations include:
- a smaller, modular design that can be customized to specific production needs
- automated or manual operation options to suit different foundry setups
- cost-effective printheads that are readily available and easier to replace
- environmentally friendly binder technology with plans to transition to a phenolic binder
- a re-coater system adapted from agricultural technologies to enhance efficiency
- an Integra operating system to ensure high reliability and remote maintenance.
This new system allows foundries to move beyond the limitations of traditional sand casting, enabling more complex geometries, reducing material costs and eliminating the need for expensive tooling and heavy post-processing.
The innovative 3D printing solution developed by Raplas and its partners is revolutionising sand casting by offering 50% faster build times compared to traditional methods and lower running costs due to reduced energy consumption and maintenance expenses. It also offers greater design flexibility for more efficient and cost-effective structures, as well as increased sustainability by minimising waste and using environmentally friendly materials.
Nigel Dowsett, Special Projects Manager at Raplas, said: "The additive manufacturing of sand moulding removes traditional constraints, enabling innovative designs and cost savings. Our solution represents a step-change for the foundry industry, making 3D sand printing more accessible and viable."
By combining cutting-edge 3D printing with deep expertise in foundry operations, this initiative is poised to transform the industry, making sand casting more efficient, sustainable and competitive on a global scale.
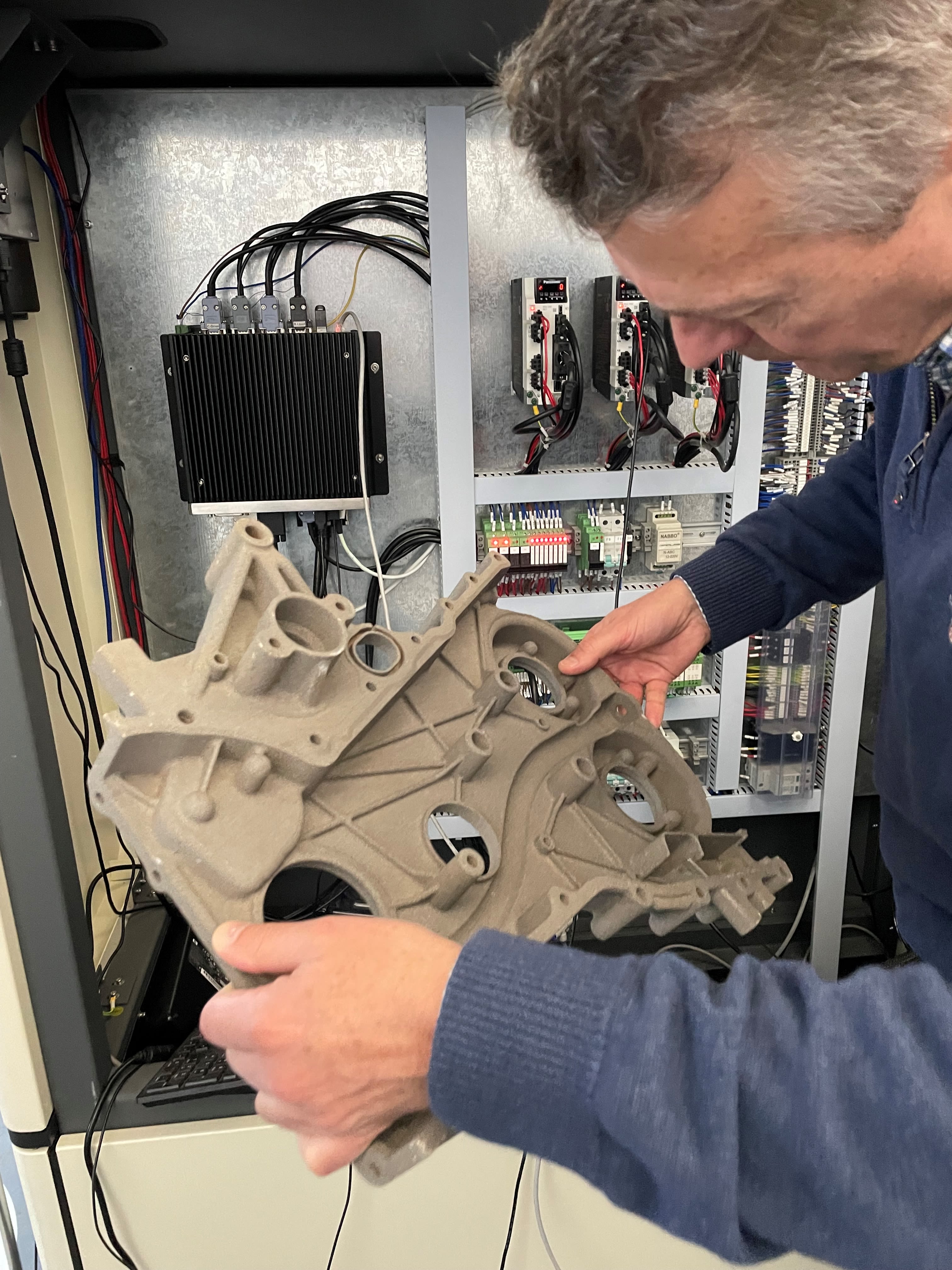
Batch Works & Matta
Matta, Batch Works and Plus X Innovation develop AI-powered Additive Manufacturing solution to improve scalability and sustainability
A collaborative research and development project has led to ground-breaking innovations in scalable and sustainable 3D printing, paving the way for more efficient and environmentally friendly manufacturing processes.
The project was led by Batch Works, an advanced circular manufacturing company, in partnership with AI software developer Matta and innovation hub Plus X Innovation and was funded through Made Smarter Innovation’s Sustainable Factories programme.
The consortium successfully developed an AI-powered automated 3D printing facility that enhances productivity, improves energy efficiency and significantly reduces waste. Key innovations include an AI computer vision system for real-time print monitoring and optimisation, autonomous hardware enabling continuous production and a digital product tracking system to enhance supply chain transparency.
These advancements directly address critical barriers to the wider adoption of 3D printing in manufacturing, such as quality control issues, high failure rates and inefficiencies in scaling production.
The automation hardware, combined with AI-driven failure detection, enables continuous, unmanned overnight printing. This has accelerated production cycles, increased manufacturing capacity and allowed skilled operators to focus on higher-value tasks.
“This project has demonstrated what can be achieved by bringing together organisations operating at the cutting edge of their fields.”
Batch Works projects that these technologies will save 40 tonnes of material over the next three years, cutting feedstock material emissions by 38 tonnes CO2e. Automated part removal has reduced energy consumption for short prints by 90%, leading to a 25% reduction in total energy usage for small parts production.
In total, Batch Works estimates a potential reduction of 1,700 tonnes of CO2e emissions over the next three years by deploying these innovations across its factories.
Beyond environmental benefits, the project has catalysed economic growth and industry innovation. It has generated four new Innovate UK spin-out projects, facilitated job creation and attracted further investment. Batch Works has established a dedicated R&D team, supporting plans for a £3 million funding round.
Matta has leveraged the project’s success to secure investment from UK, European and US stakeholders and is now exploring the application of its AI technology to other manufacturing processes, including CNC machining, robotic welding and food extrusion. Plus X Innovation has strengthened its competitive position within the workspace sector by integrating advanced prototyping and batch manufacturing capabilities.
The project’s legacy extends beyond its direct participants, fostering broader adoption of AI and automation in manufacturing. By demonstrating the viability of AI-powered 3D printing at scale, the consortium has positioned the UK as a leader in sustainable, intelligent manufacturing.
The partners are now actively pursuing commercialisation opportunities to ensure these pioneering technologies achieve widespread industry impact.
Chris Needham, Innovation Lead for Made Smarter Innovation, said: “This project has demonstrated what can be achieved by bringing together organisations operating at the cutting edge of their fields. Matta, Batch Works and Plus X Innovation created an AI-powered automated 3D printing solution which offers manufacturers an opportunity to produce parts more efficiently and sustainably. What is more, the project has generated further innovation and an enduring collaboration to spread this solution further afield.”
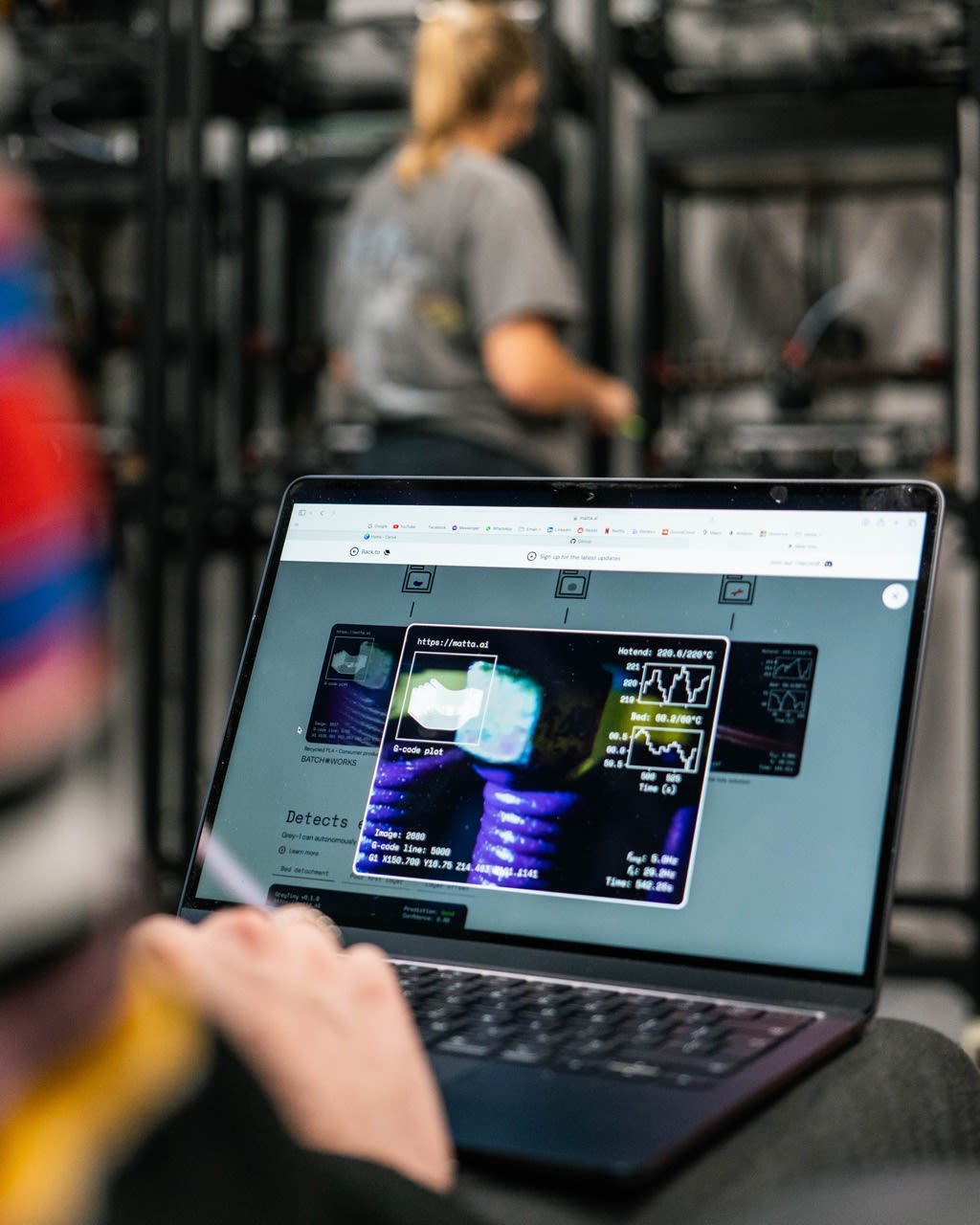
GE Spares
GE Spares unlocks innovation and net zero goals with low-cost sensor technology
GE Spares, a Londonderry-based steel manufacturer, has significantly enhanced productivity, energy efficiency and innovation through its collaboration with the Made Smarter Innovation Smart Manufacturing Data Hub (SMDH). By deploying low-cost sensors and leveraging advanced analytics, the company has gained crucial insights into its energy consumption and production processes, unlocking substantial efficiency gains.
The project involved the installation of a non-intrusive, low-cost sensor on a plasma cutting machine to monitor energy usage in real-time. The resulting dashboard provided valuable data that enabled GE Spares to assess machine utilisation and identify inefficiencies. Initial findings showed that machine availability was only 42% over a four-week period, prompting the company to explore ways to increase capacity to at least 60%.
With a clearer understanding of energy consumption patterns, GE Spares can now make data-driven decisions to optimise production scheduling and resource allocation. The company plans to expand the use of these sensors across multiple machines, providing comparative performance insights that will further enhance operational efficiency.
"...low-cost IoT devices and data analytics can support manufacturers to better understand energy usage, optimise production process and unlock opportunities for innovation across all operations."
The data-driven approach is set to reduce energy consumption by up to 15% within the first year, directly cutting operational costs while also contributing to the UK’s net zero ambitions. By identifying inefficiencies, the company can lower its carbon footprint, reducing CO2 emissions and aligning with broader sustainability goals.
Additionally, integrating energy consumption data with the company’s existing ERP system allows for precise cost analysis of production activities. This ensures accurate product pricing, maximising profitability while maintaining competitiveness in the market.
The project has initiated a cultural shift within GE Spares, fostering a data-driven mindset that supports continuous innovation. Real-time monitoring enables predictive maintenance, reducing machine downtime and improving overall equipment effectiveness. Production managers can now proactively address bottlenecks and inefficiencies, leading to a more agile and resilient manufacturing process.
By contributing anonymised data to the Manufacturing Data Exchange Platform (MDEP), GE Spares is also playing a pivotal role in advancing the wider manufacturing ecosystem. This collaborative approach enables industry peers, academia and technology partners to extract insights, develop new solutions and identify broader trends that drive sector-wide improvements.
The successful implementation of this digital strategy has paved the way for further technological advancements within GE Spares. The company anticipates long-term productivity gains of up to 50% on individual workstations, which will translate into significant overall growth. As the business evolves, the adoption of data-led decision-making is expected to generate new high-skilled job opportunities, reinforcing the company’s position at the forefront of manufacturing innovation.
Simon Coward, Programme Director for MSI’s Smart Manufacturing Data Hub, said: “Technology will play a leading role in helping energy intensive manufacturers contribute to the UK’s net zero ambitions. Working with GE Spares we have demonstrated how low-cost IoT devices and data analytics can support manufacturers to better understand energy usage, optimise production process and unlock opportunities for innovation across all operations.”
By embracing digitalisation, GE Spares demonstrates how smart manufacturing solutions can deliver transformative impact – enhancing productivity, reducing environmental impact and fostering industry-wide collaboration.
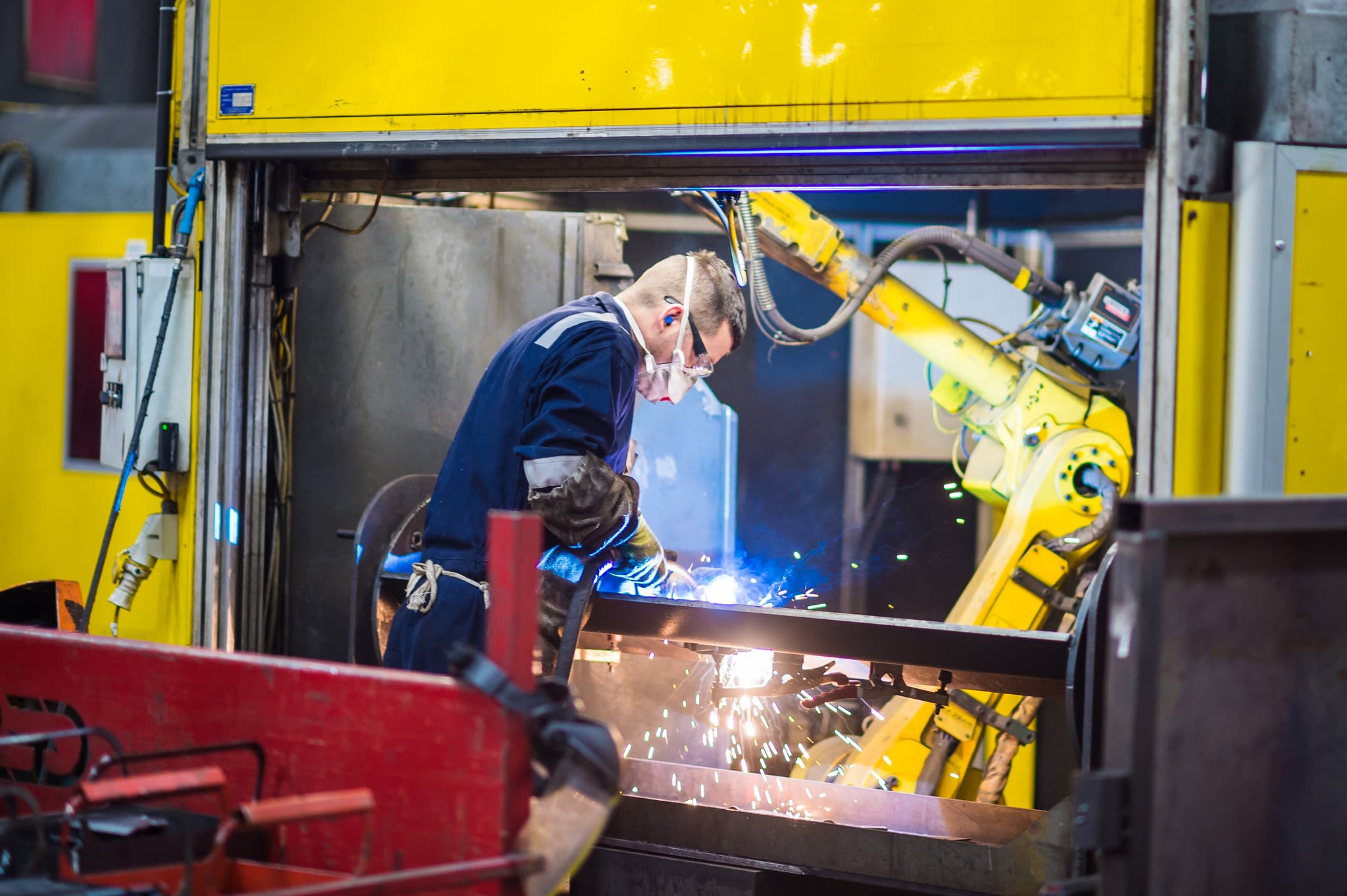
Rivelin Robotics
Robotics expert demonstrates faster, cheaper and safer method for finished 3D-printed components
Rivelin Robotics, a Sheffield-based specialist in robotic automation, has developed a transformative approach to finishing 3D-printed components, delivering enhanced productivity, cost savings and safety improvements.
In collaboration with leading manufacturers GKN Aerospace, Attenborough Dental Laboratories and Material Solutions, the CAMPFIRE (Certified Additive Manufactured Parts Finished with Intelligent Robotics Engine) project, supported by Made Smarter Innovation, has demonstrated the potential of robotic micro-factories in tightly regulated industries.
The project has developed two robotic demonstrator micro-factories powered by Rivelin’s NetShape 2.0 software platform. These micro-factories automate post-processing, reducing reliance on manual labour while improving precision and repeatability.
For Material Solutions, the robotic finishing solution reduced processing time by 28% per part and increased throughput by 50% under continuous operation. The cost per part also dropped by 24%, making automation a commercially viable option. The company is now preparing to implement the technology across multiple components in the next 12-18 months.
Attenborough Medical successfully validated the robotic finishing process, ensuring that components met strict geometric and surface finishing requirements. This development has led to the exploration of a servitised business model to facilitate broader adoption in cost-sensitive medical and dental markets.
“This project has increased our visibility in key markets, leading to new international orders and positioning Rivelin for further growth.”
By integrating machine learning, advanced sensing and robotic machining, the project enables high-precision support removal and surface finishing for aerospace, energy, medical and automotive applications. With features such as closed-loop inspection and automated rework, the NetShape 2.0 platform allows manufacturers to streamline workflows without requiring expertise in CAM, CNC or robotics.
For GKN Aerospace, the trials reinforced the potential of robotic post-processing to enhance repeatability and reduce human intervention. While delays affected the initial aerospace demonstrations, the findings supported further system improvements, culminating in a sale to a leading aerospace corporation. Additionally, Rivelin has secured a deal with an automotive manufacturer and is in advanced discussions with another aerospace customer, marking a significant step towards commercial adoption.
The success of the CAMPFIRE project has positioned Rivelin Robotics as a leader in robotic finishing solutions, leading to international interest and increased market visibility. The company has already expanded its workforce, hiring four additional engineers to support its growth.
Robert Bush, CEO of Rivelin Robotics, said: “This project has increased our visibility in key markets, leading to new international orders and positioning Rivelin for further growth. We’re now preparing to expand our operations to meet the anticipated rise in demand for robotic solutions.”
By enabling automation in post-processing, this project not only accelerates manufacturing efficiency but also supports sustainability goals by minimising material waste and reducing energy consumption. As UK manufacturing continues to embrace digital transformation, the adoption of robotic micro-factories is set to enhance competitiveness and resilience across key industries.
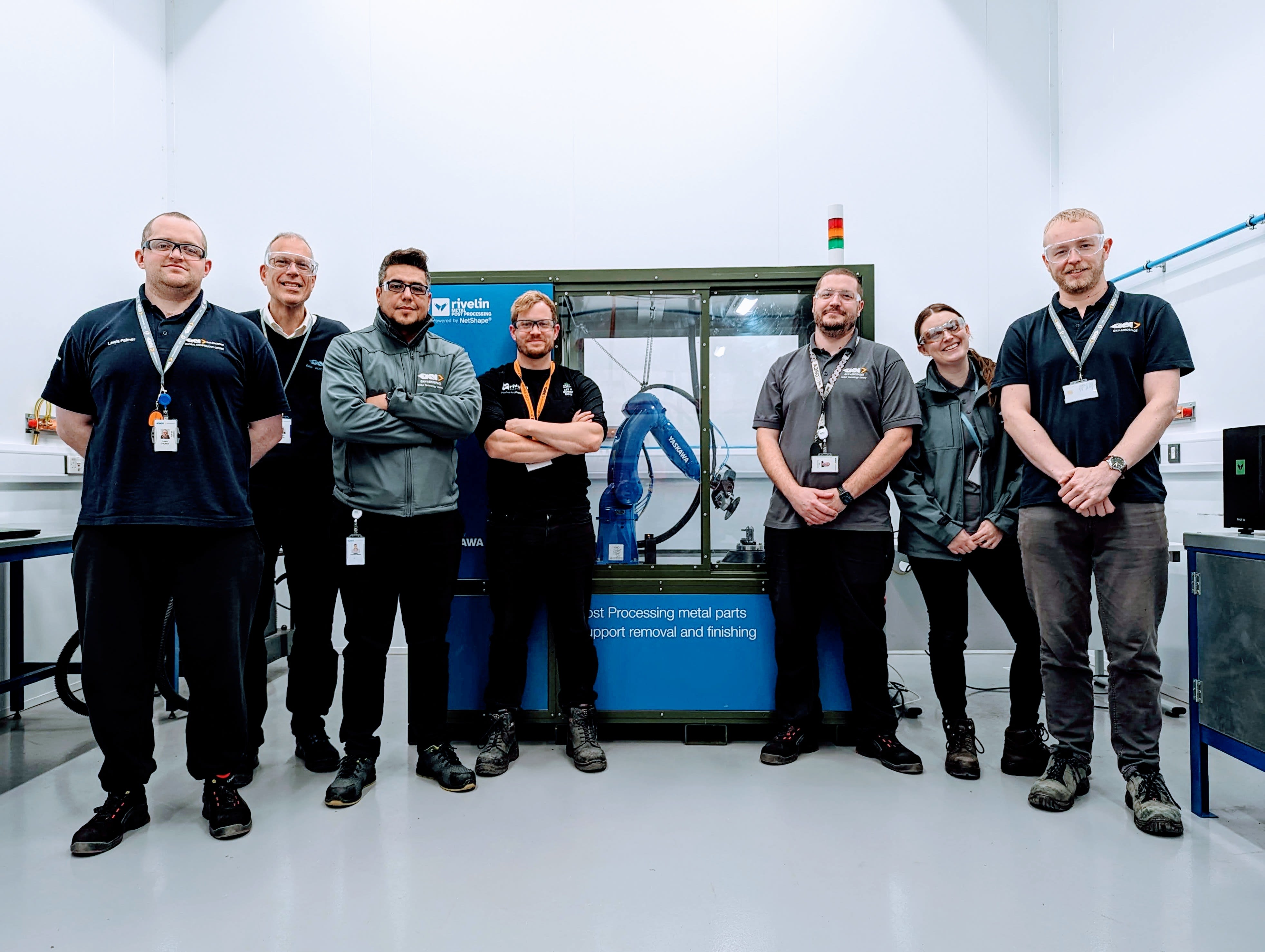