Made Smarter Innovation Challenge:
People Focus Case Studies
Empowering the workforce for a digital future
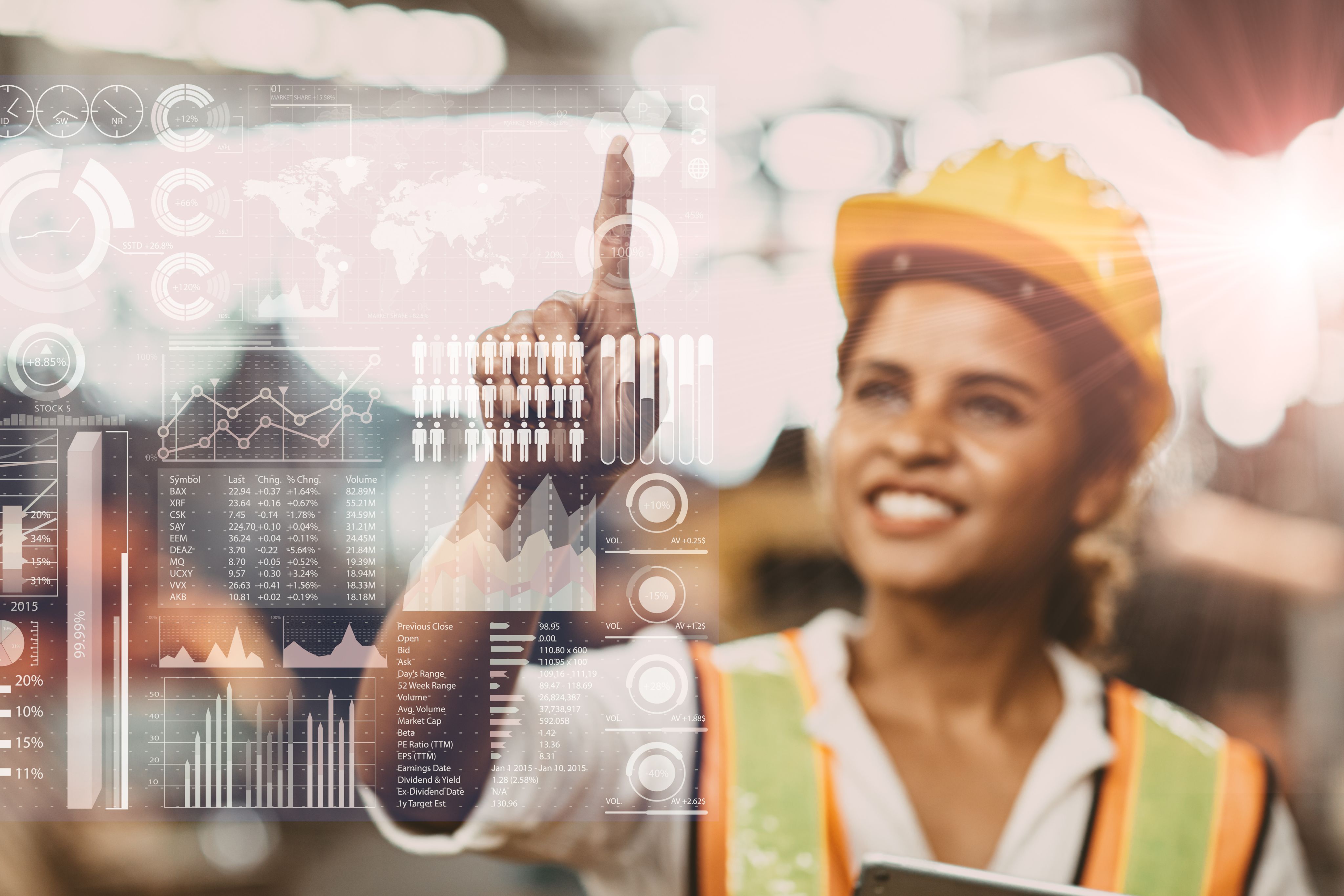
Foreword
People are at the heart of the Made Smarter Innovation (MSI) Challenge, delivered by Innovate UK, the Engineering and Physical Sciences Research Council (EPSRC) and the Economic and Social Research Council (ESRC), ensuring that digital transformation is not just about technology but also about empowering the workforce. Recognising the need for a skilled, adaptable workforce, MSI has invested in initiatives that place human capital at the centre of digitalisation. By integrating social sciences with technical research, the challenge has supported manufacturers in developing inclusive and effective digital strategies.
Through investments such as the InterAct Network and the Centre for People-Led Digitalisation, MSI has explored the human factors shaping industrial digitalisation. These initiatives have provided businesses with insights and tools to enhance workforce engagement, digital adoption and organisational change. By fostering diversity and collaboration, the challenge is ensuring that digital technologies are accessible, beneficial and widely adopted across the industry.
With over 400 organisations engaged, including a high proportion of SMEs, MSI is driving a transformation in both technology and the culture of UK manufacturing. By equipping people with the skills and knowledge to thrive in a digital landscape, the challenge is building a resilient, innovative and inclusive future for the sector.
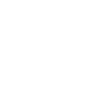
Centre for People-Led Digitalisation
Innovative neurodiversity research tackles productivity and skills challenges
Research supported by Made Smarter Innovation is driving a new approach to addressing productivity and skills challenges within industry through digital technology and neurodiversity. A collaboration between the Centre for People-Led Digitalisation (P-LD) and BIM4Water has demonstrated the benefits of digital solutions for neurodivergent individuals, businesses and wider society.
Funded by Made Smarter Innovation and delivered by researchers at Bath, Nottingham and Loughborough universities, the initiative has led to further research, new digital tools and increased industry awareness. The work is helping UK manufacturers embrace digitalisation while promoting equality, diversity and inclusion in the workplace.
Digital technologies are pivotal in transforming industry; however, challenges such as the digital skills gap and labour shortages persist. A digitally engaged workforce is essential to unlocking the full potential of digitalisation, yet neurodivergent individuals remain an underutilised talent pool. With strengths in creativity, productivity and STEM fields, this group represents a significant opportunity for addressing industry challenges, but employment levels remain low, with up to 70% of neurodivergent people unemployed or underemployed.
To explore how digital innovation can foster change, P-LD and BIM4Water conducted research aimed at enhancing employment prospects for neurodivergent individuals. The project investigated how digital technology can create equitable workplaces, with solutions designed by University of Bath undergraduate Sam Stephens. His work included AI tools to improve email accessibility, visual content for ADHD users and gamified tasks to enhance engagement. These innovations were tested by industry professionals, gaining recognition at conferences such as Digital Construction Week 2023, and earning Sam the Geoff Herrington Medal and Innovation Award.
"The future of manufacturing might be driven by technology, but it will be powered by people."
This research has since led to further opportunities, including the appointment of two doctoral studentships. Matthew Punter is exploring digital solutions to address the autism employment gap, while George Bentley is investigating workplace digital burnout, focusing on autistic individuals. In addition, a student internship was funded to analyse labour force and neurodiversity data, revealing that only 37% of neurodivergent individuals are in employment, compared to 80% of neurotypical individuals. Findings were published in a leading academic journal, highlighting the role of flexible and homeworking practices in improving employment outcomes.
P-LD has also contributed to the development of SOFA (Stories Online for Autism), a mobile app co-developed by the Centre for Applied Autism Research at the University of Bath. Initially designed to support autistic children, the next phase will focus on helping autistic adults navigate the workplace, further increasing neurodivergent employment rates.
This research has generated valuable insights and practical tools that benefit both neurodivergent individuals and wider industry. By embedding inclusive practices, fostering industry partnerships and supporting HR teams, P-LD is playing a crucial role in closing the neurodiversity employment gap. These efforts are now driving the development of a new digital tool to further support neurodivergent workers and establish more equitable workplaces.
Sherrie Rad, Innovation Lead for Made Smarter Innovation, said: “The future of manufacturing might be driven by technology, but it will be powered by people. The P-LD has brought academia and industry together to generate and implement people-led solutions that enable UK manufacturers to embrace digitalisation with confidence. Its work on increasing equality, diversity and inclusion in the workplace is an exemplar of what can be achieved through collaboration.”
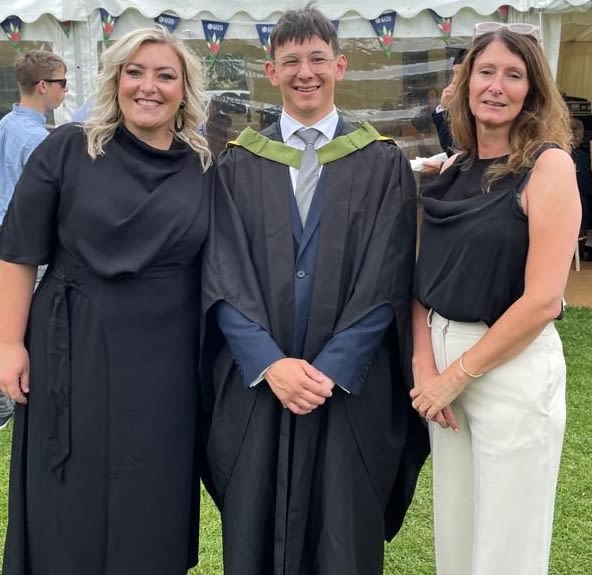
InterAct Network
Innovative research into international perception of manufacturing tackles sector’s underlying PR and productivity problems
Research funded by Made Smarter Innovation is shaping new public and policy initiatives to address the UK’s manufacturing skills challenges. A study led by InterAct, a team of economic and social scientists, highlights how sustained public engagement and collaborative policy efforts can help create a diverse and skilled workforce.
Delivered by the Made Smarter Innovation-funded research centre at Loughborough, Strathclyde and Sheffield Universities, the research calls for further studies and increased public and industry engagement to capitalise on a growing interest in manufacturing.
InterAct brings together economic and social scientists, UK manufacturers, and digital technology providers to address human challenges in industry. Recognising that technology alone is insufficient, the initiative seeks to integrate societal knowledge to fully realise digitalisation’s benefits. By fostering collaborations between academia, industry and policymakers, InterAct aims to strengthen UK manufacturing through digital innovation and interdisciplinary research.
Manufacturing once played a central role in the UK’s economy but has declined due to offshoring, reduced industrial policy focus and slow technology adoption. While the UK remains a significant manufacturing economy, it now ranks 12th globally in terms of volume contribution to the economy. The sector faces a persistent skills shortage and struggles with outdated public perceptions of factory work as labour-intensive and unattractive.
Recent global events, including the 2008 financial crisis and the COVID-19 pandemic, have renewed attention on manufacturing’s importance. While the US has responded with major stimulus initiatives, the UK has taken a policy-driven approach, introducing an Industrial Strategy to revitalise the sector. In response, InterAct’s 2022 study surveyed 2,107 UK residents to assess public perceptions of manufacturing. The results showed that, despite recognising manufacturing’s economic value, many held outdated views that made the sector seem undesirable.
"InterAct seeks to pioneer human insight for industry and bring together academics from the social sciences to support the innovation and diffusion of digital technologies."
To explore global attitudes toward manufacturing, researchers from the University of Cambridge and Aston University conducted a comparative study across seven industrialised nations. Their review of 68 policy strategies identified key trends shaping manufacturing’s future: digitalisation, sustainability and skills development. The research found that countries such as Germany and the US have stronger manufacturing reputations, with 75% of respondents seeing the sector as vital to the economy, compared to just 40% in the UK.
Findings emphasised the need for targeted policy initiatives, including systematic data collection on public perceptions, measurable diversity targets and improved education on manufacturing careers. The research has influenced an ongoing Department for Business and Trade project on defining the true value of manufacturing.
Insights from the study have been widely shared with policymakers, trade bodies and industry stakeholders through conferences, workshops and webinars. Notably, the research was showcased at the 2023 Women in Manufacturing conference and an international perceptions workshop at Aston Business School, sparking further collaborations to reshape manufacturing’s public image. By addressing misconceptions and policy gaps, this research is paving the way for a more inclusive and resilient UK manufacturing sector.
Professor Jillian MacBryde of the University of Strathclyde, Co-Director of InterAct, said: “InterAct seeks to pioneer human insight for industry and bring together academics from the social sciences to support the innovation and diffusion of digital technologies that will result in a stronger, more resilient UK manufacturing industry.
“The outcomes of this strand of research are precisely the reason why collaborations between academia, industry and policymakers are vital to build a strong, vibrant, interdisciplinary community to support the digitalisation of UK manufacturing.”
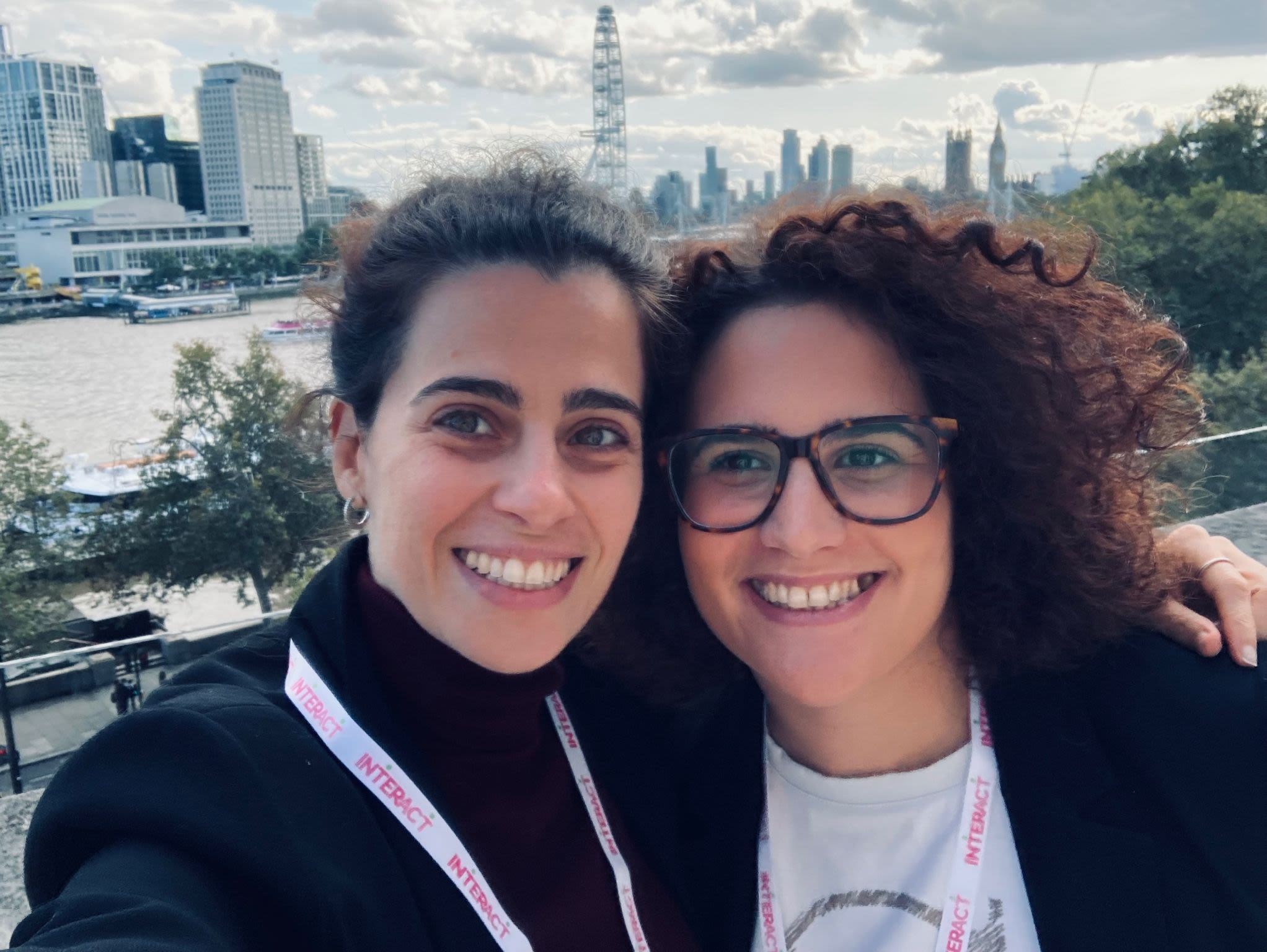
Autolomous
Empowering the NHS advanced therapies ordering prototype IT system with manufacturing insight from an electronic batch manufacturing system
Advanced Therapy Medicinal Products (ATMPs) – also known as gene or cell therapies – are at the cutting edge of personalised medicines. They are driving remarkable changes in clinical practice across multiple fields of medicine, including new cancer therapies, regenerative treatments and enhanced wound healing. However, they are also very expensive, often costing hundreds of thousands of pounds to millions of pounds per treatment.
This is because many ATMPs are made from a patient’s own cells. While this bespoke production creates a truly personalised medicine, it means the manufacture and supply of advanced therapies is uniquely challenging.
“Making ATMPs is very different from paracetamol or vaccines, for example. Each batch needs to be tested, approved and the manufacturing data captured, but whereas ordinary medicines can be made in batches of 100,000+ in one manufacturing run, each batch of ATMP only produces one treatment,” said Kwok Pang, COO of Autolomous, a company that designs software solutions for the ATMP supply chain. “It’s a major challenge for both manufacturers and the NHS to deliver the process at scale.”
With £500,000 funding from the Made Smarter Innovation Challenge, Autolomous led a project with the Advanced Therapies Facility, University of Birmingham and the University Hospitals Birmingham NHS Foundation Trust to integrate its software platform AutoloMATE to the NHS protype advanced therapy ordering system that streamlines the scheduling and ordering system for ATMPs.
“Increased efficiency along the value chain can drive down costs and help create a better understanding of the product, all of which will help cure more patients in future.”
Creating an advanced therapy requires a drug company to organise the collection of patient cells, transfer them to a manufacturing site where they undergo a complex manufacturing process, and then precisely time the delivery of the therapy back to the hospital in time to treat the patient.
“Currently, the scheduling is largely managed and organised by individuals using diaries, white boards and emails being sent back and forth. In addition, they are dealing with a live cell product, which leads to unpredictability in the supply chain. And on top of all that, there is no margin of error in this type of manufacturing; the wrong product to a patient could kill them,” said Pang. “To account for all these considerations, current schedules allow large buffers of time. It means the manufacturing teams cannot work at full production capability.”
By creating an interface between these systems, AutoloMATE aims to increase efficiency and maximise production capacity – enabling greater quantities of advanced therapies to be produced, and at a lower cost.
The project builds on and integrates existing technology developed by the Advanced Therapies Treatment Centres initiative funded by UKRI. In this project, the integrated platforms demonstrated an 85% reduction in scheduling and 50% reduction in manufacturing time. “Importantly, because it removes so many of the manual elements, it also improves the overall safety profile of these complex medicines. This is key to demonstrating to regulators that scaling up can be achieved with no increase in risk,” said Pang.
Moving forward, Autolomous is working to demonstrate the platform could be rolled out across NHS centres of excellence. “This is a fast-growing sector, with more than 2,000 clinical trials in progress for personalised medicines – and some of these are for treating diseases with much larger patient populations,” said Pang.
“Digitisation frees up production capacity and optimises the skills of those working in the industry. Increased efficiency along the value chain can drive down costs and help create a better understanding of the product, all of which will help cure more patients in future.”
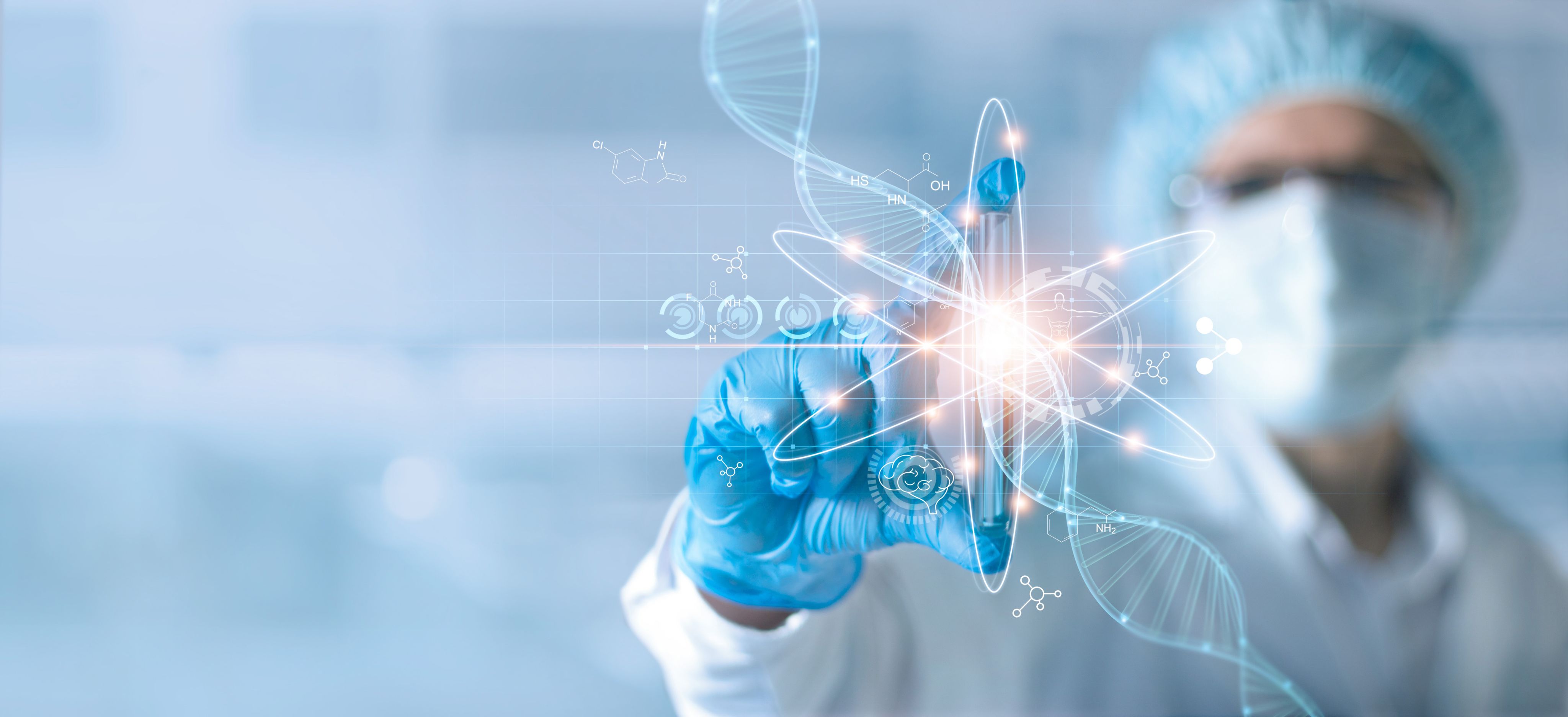
Harrison Spinks & BACS
Spinks and BACS collaboration transforms traditional spring manufacturing process using digitisation, automation and analytics
Harrison Spinks Products (Spinks), a UK-based spring component manufacturer, has achieved significant gains in productivity, waste reduction and energy efficiency through a collaborative R&D project with Bespoke Automation Controls Solutions (BACS) and the Manufacturing Technology Centre (MTC). Supported by Made Smarter Innovation, the project introduced IIOT technologies, networking, machine learning and analytics to modernise a traditionally manual wire-drawing process.
Crucially, the automation has enabled Spinks's skilled engineers to spend less time on manual work and more on high-value activities. The company's senior management has been up-skilled, too. Managers are now using Spinks's ERP (enterprise resource planning) system, which has been integrated with an HMI (human-machine interface) on the shop floor, to access and analyse performance data to identify issues with wire quality.
By digitising and automating this process, the company increased overall equipment effectiveness (OEE) by 25%, reduced waste by 56% and lowered energy consumption by 4%. These improvements have accelerated plans to expand the solution across additional production lines.
Spinks manufactures micro coils for mattresses through a wire-drawing process that reduces a wire’s diameter by pulling it through dies. This traditional method was highly manual, leading to inefficiencies, material waste and delayed quality control. With six production lines drawing high-carbon steel rod into wire as fine as 0.67mm, the company sought to improve accuracy, efficiency and sustainability.
The partnership with BACS and MTC aimed to optimise process control, reduce downtime and minimise material loss through real-time monitoring and digital automation.
The MTC conducted process mapping and sensor selection to identify key areas for digital optimisation. Advanced modelling techniques analysed thermal behaviour, energy consumption and die wear to determine efficiency improvements.
“Wire drawing is a very traditional industry. This project has automated a very manual, inefficient process, and freed up our very capable engineers to focus on more high value tasks.”
BACS designed and implemented the software architecture, network infrastructure and dashboard system, integrating data analytics with Spinks’ enterprise resource planning (ERP) system. The final solution included:
- six custom control panels and 68 sensors to monitor real-time production data
- Raspberry Pi devices for data collection and edge computing
- 37 current clamps, seven dashboards and three IoT gateways to enhance process visibility
- cloud-based monitoring tools enabling remote access to performance metrics.
The system captured previously unavailable data, such as temperature, tooling alignment and power draw, providing critical insights for process optimisation.
The implementation of automation and real-time data analytics led to significant operational improvements:
- 25% increase in OEE, improving overall efficiency
- 75% reduction in die changeovers, extending die lifespan and reducing downtime
- 56% decrease in scrap waste, minimising material losses
- 4.3% reduction in energy consumption, with potential for greater savings through refined monitoring
- 33% reduction in die changeover time, improving production flow.
With improved monitoring, leadership can now analyse production trends and identify quality issues faster. Spinks is also developing a prototype demonstrator of the wire-drawing line for training and industry engagement, positioning itself at the forefront of digital manufacturing innovation.
Richard Essery, Director of Sustainability and Innovation at Spinks, said: “Wire drawing is a very traditional industry. This project has automated a very manual, inefficient process, and freed up our very capable engineers to focus on more high value tasks.”
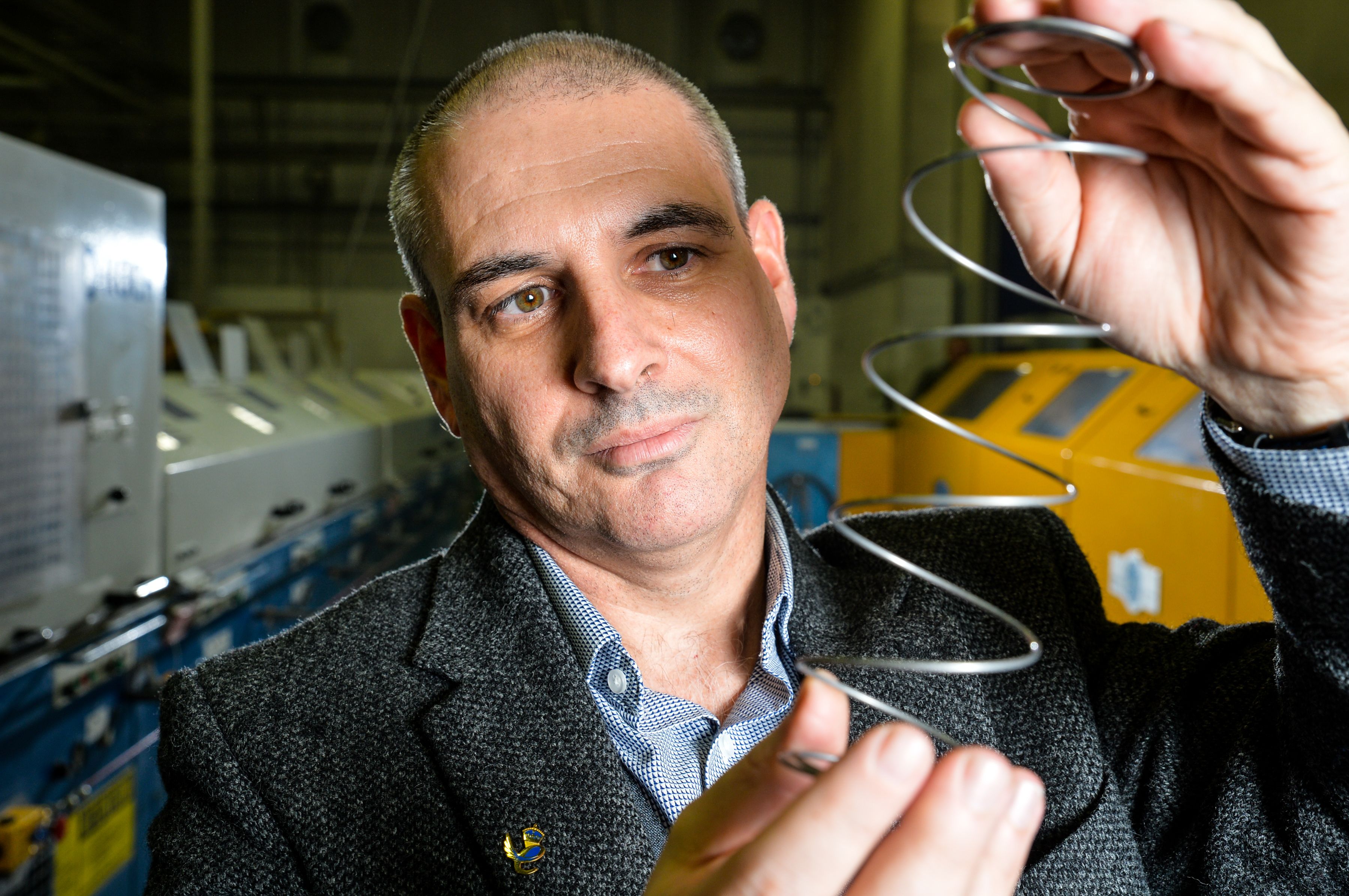
Intellium AI
Intellium’s innovative AI tool transforms manufacturing workforce into citizen data scientists to achieve productivity and sustainability gains
A groundbreaking AI enterprise platform is transforming manufacturing by generating actionable insights that enhance productivity and accelerate net zero goals. Developed by Bristol-based Intellium AI, BoostBot was created in collaboration with GKN Aerospace as part of Project Butterfly, supported by Made Smarter Innovation’s Sustainable Smart Factory programme.
BoostBot uses generative AI to streamline complex manufacturing analysis, translating intricate data into easy-to-understand insights. This enables engineers and operators to optimise processes efficiently, driving sustainability and operational excellence. The solution addresses key industry challenges, including the adoption of AI in manufacturing, upskilling the workforce and improving resource efficiency.
By applying advanced predictive modelling, process optimisation and real-time monitoring, BoostBot enables manufacturers to reduce energy consumption, enhance material efficiency and lower emissions. The system captures and analyses both real-time and historical data, using machine learning to provide predictive and prescriptive actions, all accessible through a user-friendly interface.
The impact of BoostBot has been significant. In its application to aircraft window coating, AI identified key parameters to enhance consistency, reducing CO2e emissions by 5% – equivalent to 20,000kg per year. Similarly, in analysing ribs cycle times, AI pinpointed inefficiencies, leading to a 5% increase in resource efficiency and a CO2e reduction of 13,717kg per year.
“BoostBot puts AI in the hands of engineers and operators as another tool in their toolkit, effectively turning them into citizen data scientists."
This innovation not only enhances operational sustainability but also supports workforce development by embedding AI capabilities within engineering teams. By making AI-driven insights accessible without requiring coding expertise, BoostBot empowers operators to make data-informed decisions, fostering a more skilled and digitally engaged workforce.
Following the success of its implementation at GKN Aerospace, discussions are underway to expand BoostBot’s application to additional manufacturing processes. Intellium AI is also engaging with companies in aerospace and naval sectors, further extending the platform’s impact across industries.
As a result of its growth, Intellium AI has expanded its team, reinforcing its commitment to advancing AI adoption in manufacturing.
Intellium AI’s CEO, Kiran Krishnamurthy, said: “BoostBot puts AI in the hands of engineers and operators as another tool in their toolkit, effectively turning them into citizen data scientists. Our solution accelerates the adoption of AI across a range of businesses, from large OEMs to SMEs, by delivering value through democratised analysis of IoT data related to cycle times and manufacturing process parameters.”
BoostBot exemplifies the potential of AI to drive digital transformation, enhance manufacturing efficiency and support the UK’s net zero ambitions. By combining cutting-edge technology with human expertise, this innovation paves the way for a more sustainable and competitive manufacturing sector.
Chris Needham, Innovation Lead in the Made Smarter Innovation Challenge, said: “Intellium AI has clearly demonstrated industry insight and innovation can leverage data and make a significant difference to manufacturing business, while developing a skilled, digital-savvy and engaged workforce.”
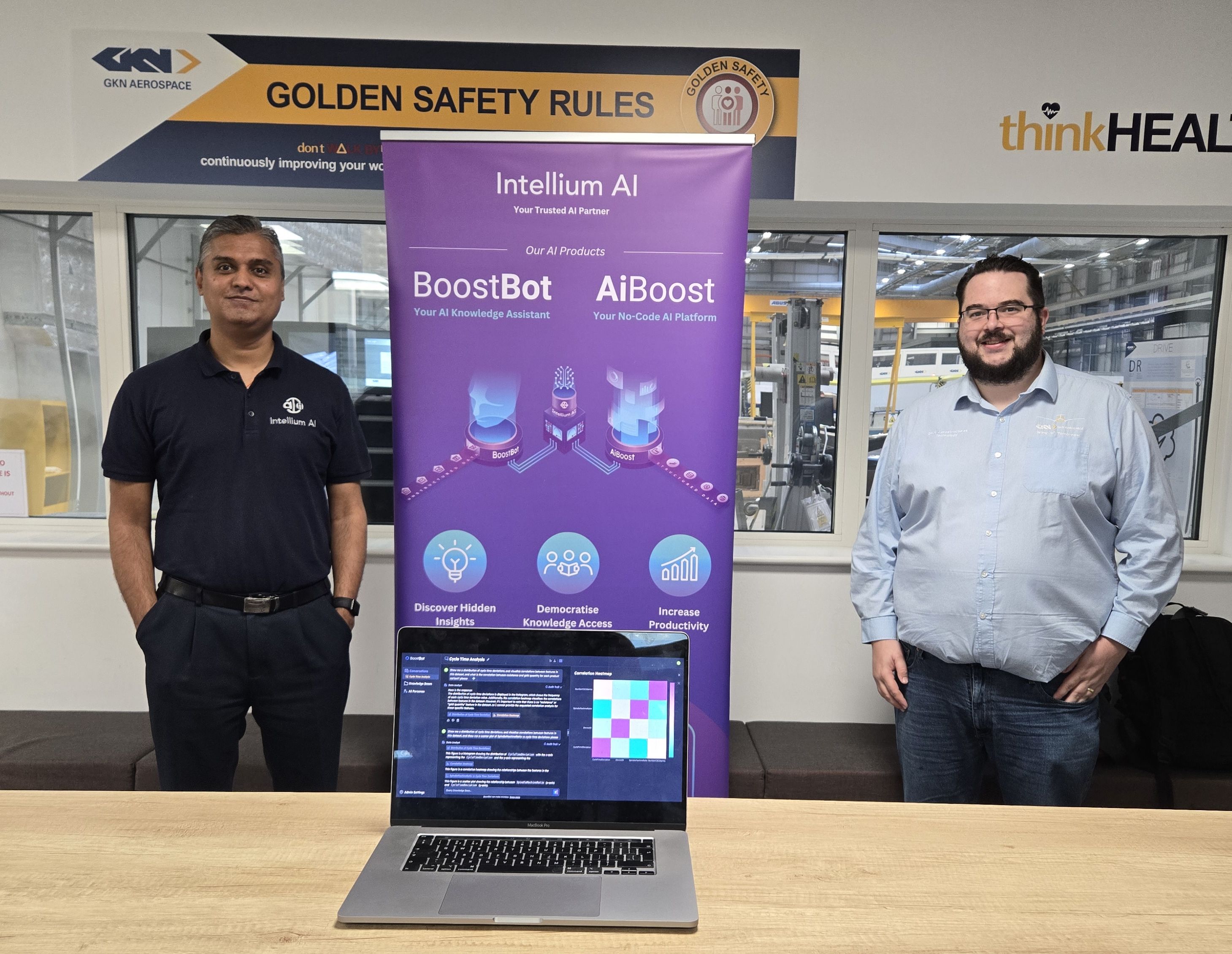
Raynor Foods
A prototype software platform offers food manufacturers the opportunity to securely share valuable data – increasing productivity, improving cashflow, boosting food quality and reducing waste within the supply chain
A pre-packed sandwich relies on a precise supply chain, maintaining strict temperature control and timing. Any mismatch between supply and demand risks significant waste. Safety is critical, as shown by a recent fatal allergy case. The Digital Sandwich project aims to bring increased traceability, security and accountability to the food supply chain by using the latest industrial digital technologies.
“Currently, very little data is shared up and down the supply chain. It not only means different components may not be working in tandem with each other, but also that important information – such as food safety and regulatory data – can be difficult to access quickly,” said Tom Hollands, Innovation and Technical Director at Raynor Foods, a leading UK pre-packed sandwich business, which is leading the project.
“The combination of technologies in Digital Sandwich enables detailed data to be shared across the complex supply chain, which lead to increased productivity, improve cashflow, help boost food quality and reduce the £15 billion of food waste each year within in the supply chain.”
With £4 million funding from the Made Smarter Innovation Challenge, Raynor Foods brought together a large consortium of food manufacturers, supply chain partners, suppliers, technology developers and universities. Using Raynor Foods’ sandwich supply chain as a use case, the project created a ‘sandwich’ of digital technologies – including internet of things (IoT), blockchain and AI – into one unique platform.
“This type of information exchange can increase productivity, improve cashflow, help boost food quality and reduce the £15 billion of food waste each year within in the supply chain.”
“The world-first combination of technologies provides information at a granular level with the whole history of a product from primary production to point of sale,” said Oliver Kinsey, Innovation Delivery Manager at IMS Evolve, lead IoT developer and project partner. “Every item of food will have a digital identity that’s securely locked into the blockchain. For example, a manufacturer could scan a ham and the platform has data that tracks it to an individual pig identification tag on a farm and shows where it was slaughtered. Information that we collect from sensors on fridges show the product has been kept at safe temperatures and trackers on delivery trucks indicate when it will arrive at the factory.”
As well as clear benefits in terms of ingredients’ traceability, the platform also helps maximise efficiency and reduce waste. “Sandwich production is particularly vulnerable to the Bullwhip Effect, where a small change at one end of the supply chain, can lead to increasing changes as it moves through. An increase in orders for BLTs from one retailer, for example, causes a sandwich manufacturer to increase its production by a bit more to compensate, which then causes the bacon, lettuce and tomato suppliers to increase even more – and much of this food is wasted,” said Hollands. “Digital Sandwich reduces this effect by enabling instant, real-time data to flow through the whole supply chain.”
Importantly, the platform allows small and medium sized enterprises, who don’t usually have access to this kind of technology, to benefit – enabling every point of a supply chain to be optimised, from the smallest producer to largest multinational.
The Digital Sandwich has potential application beyond food manufacturing, too. “It could benefit any sector with complex, fast moving supply chains that demand a high level of trust, such as pharmaceuticals, aerospace and automotive,” said Hollands. “If this technology was widely adopted by UK Plc it would have a profound and positive impact on the economy.”
Since completing its demonstrator platform, Raynor Foods has led a follow-on project that aims to reduce the carbon footprint of food manufacturing. The project, S3 (Smart People, Smart Process, Smart Factory), enables factories to present data (e.g. on waste management and greenhouse gas emissions) gained from real-time monitoring in a ‘gamified’ form. Factory floor staff are thus empowered to act on the data and have their interventions evaluated to earn ‘in-game’ rewards. By actively involving staff in process optimisation, the project underscores the essential role of people in achieving sustainable manufacturing practices.
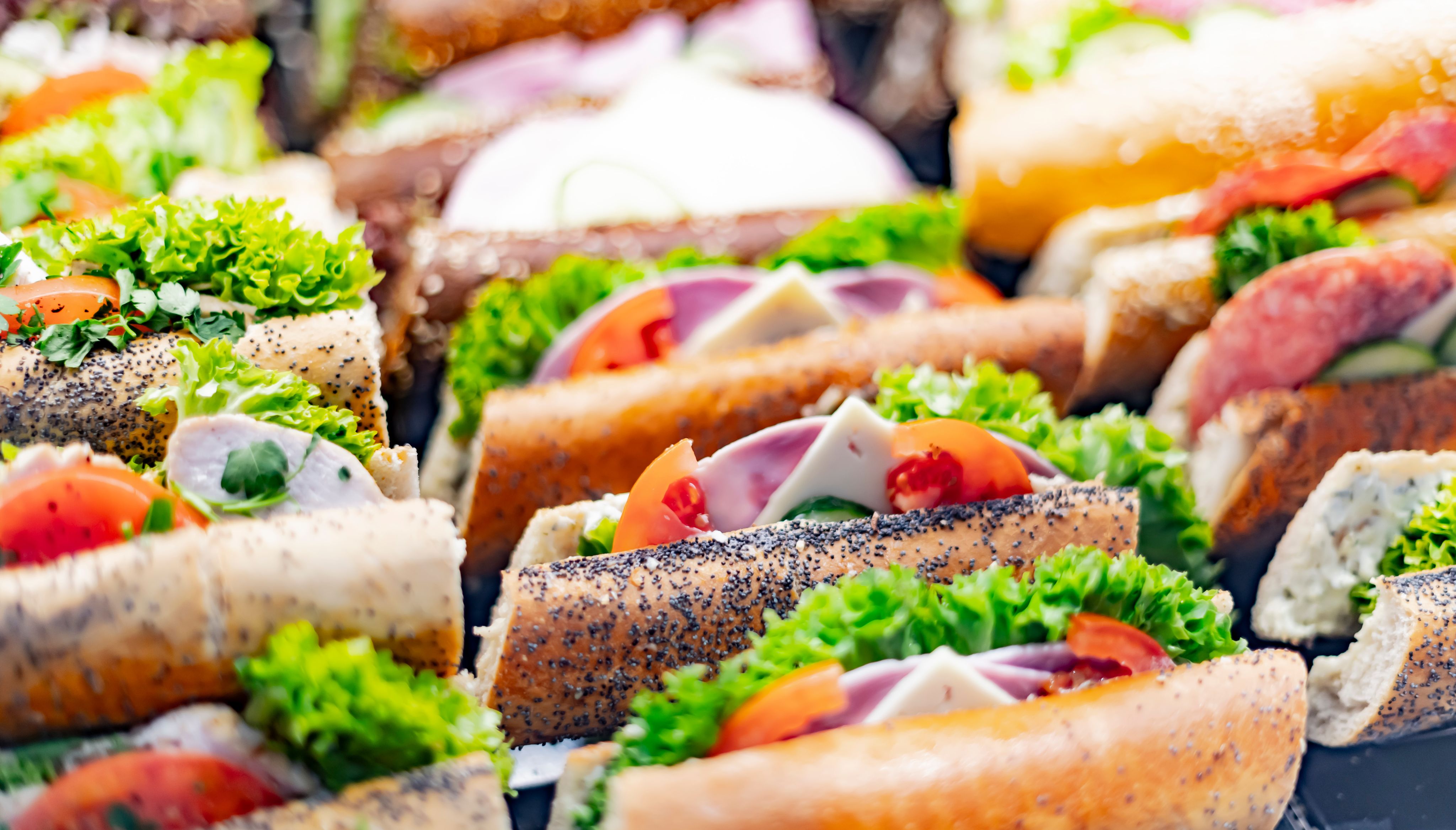