Made Smarter Innovation Challenge:
Net Zero Focus Case Studies
Powering a sustainable future through digital innovation
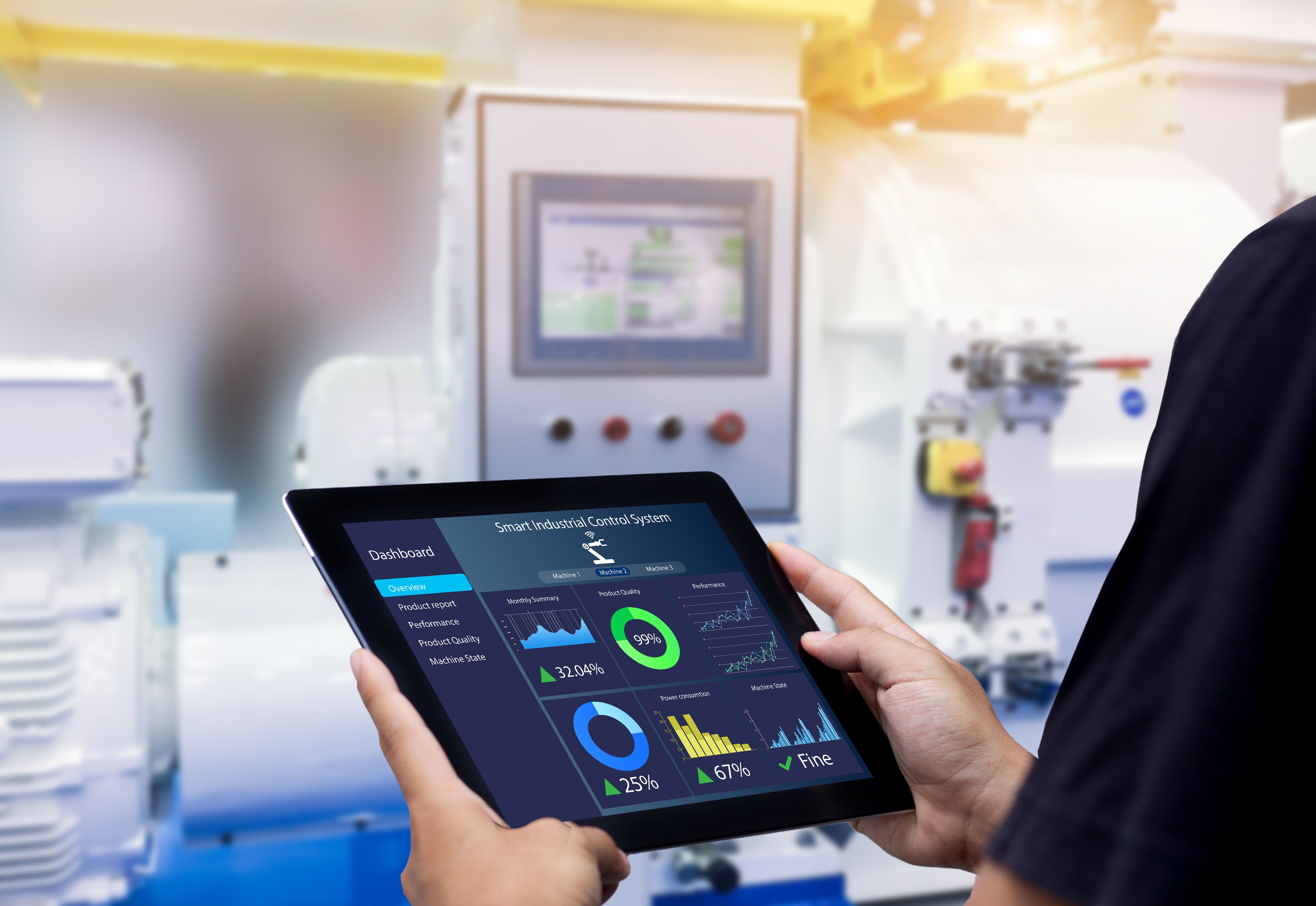
Foreword
The Made Smarter Innovation (MSI) Challenge, delivered by Innovate UK, the Engineering and Physical Sciences Research Council (EPSRC) and the Economic and Social Research Council (ESRC), is driving the UK towards a more sustainable manufacturing future by harnessing digital technologies to reduce carbon emissions and waste.
Since its launch in 2020, MSI has focused on enabling smarter, more efficient processes that support the UK's transition to Net Zero. With targeted investments in AI, data analytics, robotics and connectivity, manufacturers have been empowered to develop and adopt solutions that minimise environmental impact while maintaining competitiveness.
From smart factories leveraging real-time data to reduce energy consumption to supply chains that optimise material use, the challenge has created opportunities for businesses to align with the UK’s Industrial Decarbonisation Strategy. Notably, the Sustainability in Manufacturing Accelerator and the Sustainable Smart Factory funding calls have helped companies integrate resource efficiency into their operations. These initiatives contribute to the MSI objectives of a 4.5% reduction in UK carbon emissions and a 25% decrease in manufacturing waste.
By supporting digitalisation in manufacturing, the MSI Challenge is enabling a more circular economy – one where sustainable production methods lead to increased resource reuse and a lower environmental footprint. As we move forward, MSI remains committed to fostering innovation that aligns with Net Zero ambitions, ensuring UK industry plays a leading role in global sustainability efforts.
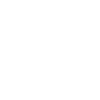
SupplyVue
The development of a digital platform could enable manufacturers to measure and model the carbon impact of every aspect of their supply chains
Traditionally, supply chain decisions are based on the three pillars of cost, quality and service, but if manufacturers are to meet the challenges of delivering Net Zero, they need to add another pillar: carbon footprint.
“While some businesses are incorporating carbon measurements, it tends to be done for annual reports or certain aspects of production. There’s no capability for measuring carbon in a joined-up way through a whole supply chain,” said Andy Birtwistle, CEO of supply chain technology developer SupplyVue.
SupplyVue is leading a project that aims to make carbon a central tenet of supply chain management. Using £1.5 million funding from the Made Smarter Innovation Challenge, it is working with industry, technology and academic partners to develop a new digital platform, CarbonVue, that will provide visibility of carbon throughout a supply chain, enabling integrated real time carbon and productivity management.
The project builds on SupplyVue’s technology, which builds a digital twin of a supply chain. By modelling different scenarios, businesses can identify opportunities for efficiencies and make more informed decisions about future strategies.
“With CarbonVue, we are building the capability to add carbon impact to our technology platform, enabling the measuring and modelling of each individual supply chain activity, such as the energy used by a particular machine or a lorry delivery to different destinations,” said Birtwistle. “It will generate an absolute measure of carbon per kilogramme of product – much like the calorie measure of food.”
“This technology has the capability to unify supply chain partners in a common low carbon goal.”
The project is using real supply chain data from partners Tata Steel and aerospace supplier Moveero (formerly GKN), while defence company Babcock International is providing specific insights for product development from their sector and position at the top of a supply chain. The team also worked with the University of Warwick to create algorithms for analysing and modelling the supply chain.
At a time when customers are calling for greater transparency about environmental impact, alongside government targets, CarbonVue has the potential to put carbon management at the front and centre of decision making in a supply chain.
“Poor supply-chain collaboration is a barrier to end to end efficiency, but this technology has the capability to unify supply chain partners in a common low carbon goal,” said Birtwistle. “The need for the UK’s manufacturing sector to be more productive and to reduce carbon emissions is a clear imperative but improvement is slow. CarbonVue could provide the catalyst for change.”
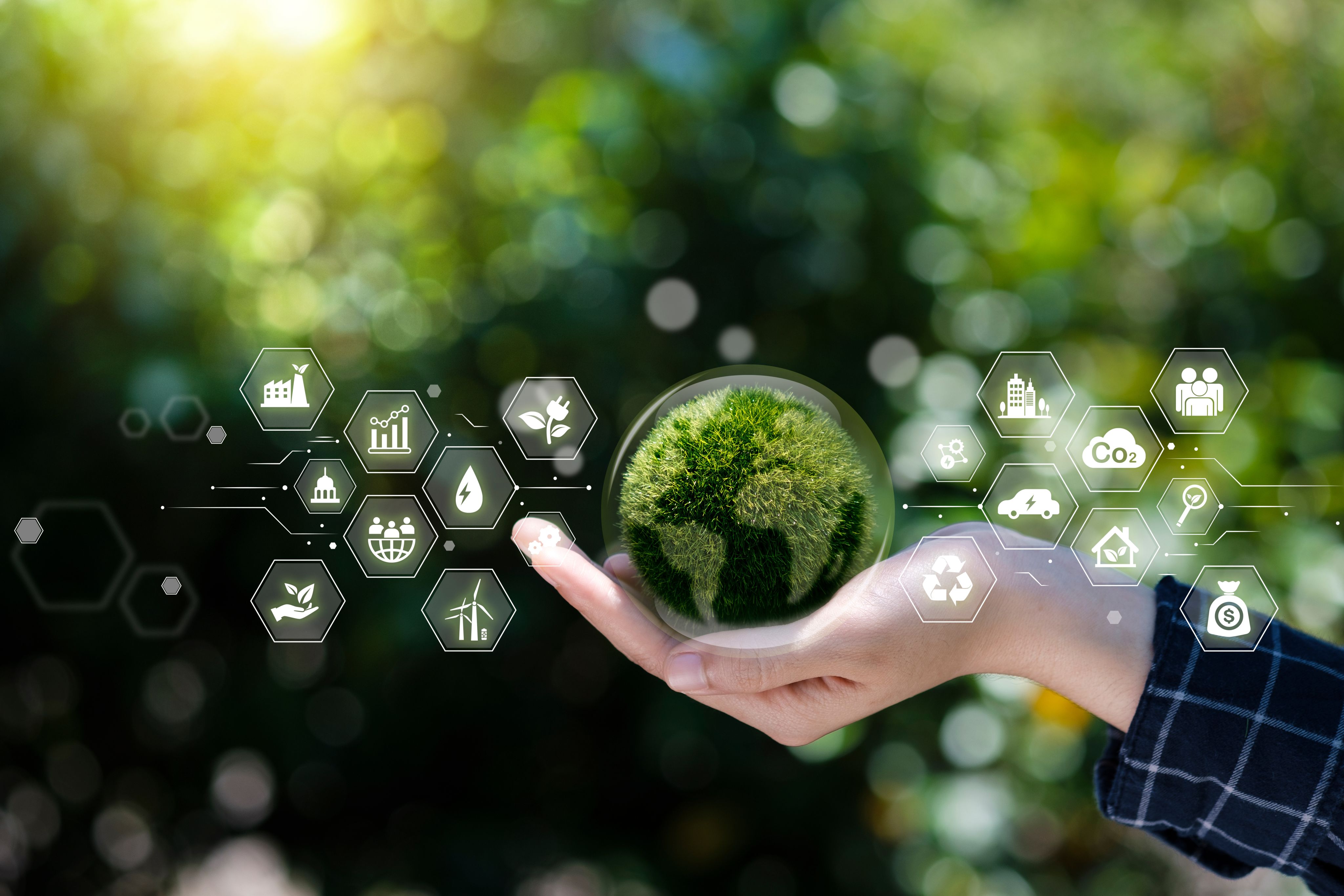
BAE & Machine Intelligence
A cutting-edge AI-driven vision inspection tool is set to enhance manufacturing productivity, resilience, and sustainability, supporting the UK’s Net Zero ambitions
Somerset-based start-up Machine Intelligence (MI) has collaborated with BAE Systems’ Air division through the Made Smarter Innovation Technology Accelerator to develop an AI solution to improve defect detection in metal joints, streamlining quality assurance and reducing waste.
By using bio-inspired machine learning, the AI system analyses X-ray images to detect defects accurately, reducing reliance on manual inspections. This improves efficiency, enhances operator confidence and minimises energy consumption – key to reducing carbon emissions.
Following successful trials, BAE Systems has implemented the technology in its inspection process and is exploring wider applications, demonstrating AI’s role in achieving sustainable manufacturing.
Susan Bowen, CEO of Digital Catapult, which leads the Technology Accelerator programme, said: “This collaboration showcases the impact of uniting tech innovators with industry leaders to advance UK manufacturing.”
Manufacturing inspections are often time-consuming and prone to human error. BAE Systems is leveraging AI to enhance accuracy, reduce waste and lower its carbon footprint. The AI system delivers rapid, explainable “go” or “no-go” decisions with minimal training data, making it scalable across various applications.
“Our technology streamlines inspections, ensuring efficiency, reliability and sustainability, driving the UK towards a Net Zero future.”
James Leadbetter, Senior Engineer at BAE Systems, said: “To compete globally, we must integrate digital tools that enhance efficiency. This collaboration is shaping our future manufacturing strategy.”
MI’s approach differs from conventional AI models by requiring fewer images to train robust machine-learning models. This makes AI adoption more accessible across industries.
Dr Simon Harding, MI's founder, said: “Our AI ensures high-quality defect detection, bridging the gap between human expertise and automation for a more sustainable future.”
With BAE Systems’ support, MI has transitioned from consultancy to product development, expanding into sectors such as aerospace and medical imaging. By integrating AI inspection, BAE Systems is reducing material waste, energy-intensive rework and emissions – directly contributing to Net Zero targets.
Dr Ben Farmer, Deputy Challenge Director for Made Smarter Innovation at Innovate UK, said: “This project demonstrates how AI can enhance productivity, resilience and Net Zero goals by solving key industry challenges.”
Dr Harding said: “Our technology streamlines inspections, ensuring efficiency, reliability and sustainability, driving the UK towards a Net Zero future.”
This AI-driven innovation highlights the success of the Made Smarter Innovation Technology Accelerator in advancing sustainable manufacturing and economic growth.
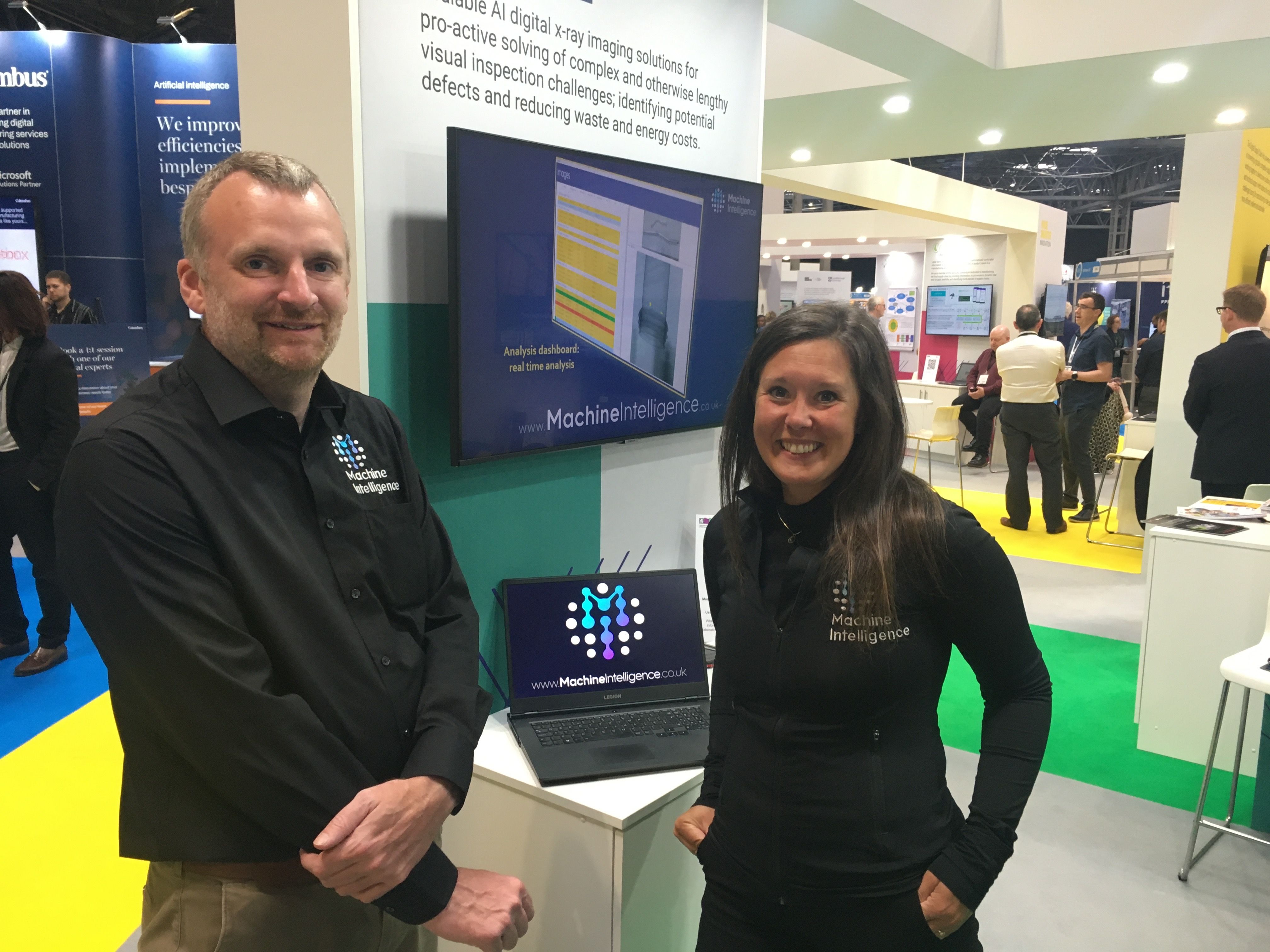
Deep.Meta
AI tool demonstrates potential for steelmakers to achieve green growth
A pioneering AI platform is helping steelmakers reduce energy consumption, lower CO2 emissions and enhance productivity, supporting the UK’s Net Zero ambitions.
London-based start-up Deep.Meta collaborated with the Materials Processing Institute, steel re-roller Spartan UK and construction firm Grosvenor as part of the Made Smarter Innovation Sustainable Smart Factory programme. The project developed and tested Deep.Meta’s Deep.Optimiser, an AI tool that analyses factory data to optimise decision-making.
The AI system has demonstrated the potential to cut energy consumption by 24 kWh per tonne of steel, reduce CO2 emissions by almost 5% and improve productivity by 20%. For a steel manufacturer producing 2 million tonnes annually, this equates to an energy reduction of 48 TWh – enough to power 3,000 UK homes per year.
Chris Needham, Innovation Lead for Made Smarter Innovation, said: “Deep.Meta’s application of AI on steelmaking, one of the world’s most energy intensive sectors, is an extraordinary example of what can be achieved by bringing together technology innovators and industry, and has far reaching potential.”
Steel production is highly energy-intensive, contributing to 8% of global CO2 emissions. One key challenge is managing furnace temperatures efficiently to prevent excessive energy use.
"If this technology were adopted across all 1,600 steel plants globally, we could reduce emissions by 500 megatons every year."
Deep.Optimiser builds a digital twin of a steel plant, integrating 40 years of production data with real-time sensor inputs to predict when steel is at the optimal temperature for processing. The system provides live recommendations via a cloud-based app, enabling operators to optimise production and reduce energy waste.
Dr Osas Omoigiade, founder of Deep.Meta, said: “Many steelmakers are not able to leverage their existing data in a way that accounts for the interdependence of their processes. With well-informed, actionable insights that account for these complexities they could significantly reduce their energy consumption and production costs.”
Deep.Optimiser has already been deployed on a UK production line, and Deep.Meta has secured investment from the US, doubling its workforce. Spartan UK has also embraced new digital processes, enhancing workforce skills and efficiency.
Dr Omoigiade said: “If this technology were adopted across all 1,600 steel plants globally, we could reduce emissions by 500 megatons every year – equivalent to a 20% decrease in the overall CO2 associated with steel production.”
By enabling steelmakers to cut costs, boost productivity and lower emissions, Deep.Optimiser represents a major step toward a more resilient and sustainable UK manufacturing sector. The success of this innovation underscores the value of industry collaboration in tackling environmental challenges while ensuring economic growth and competitiveness.
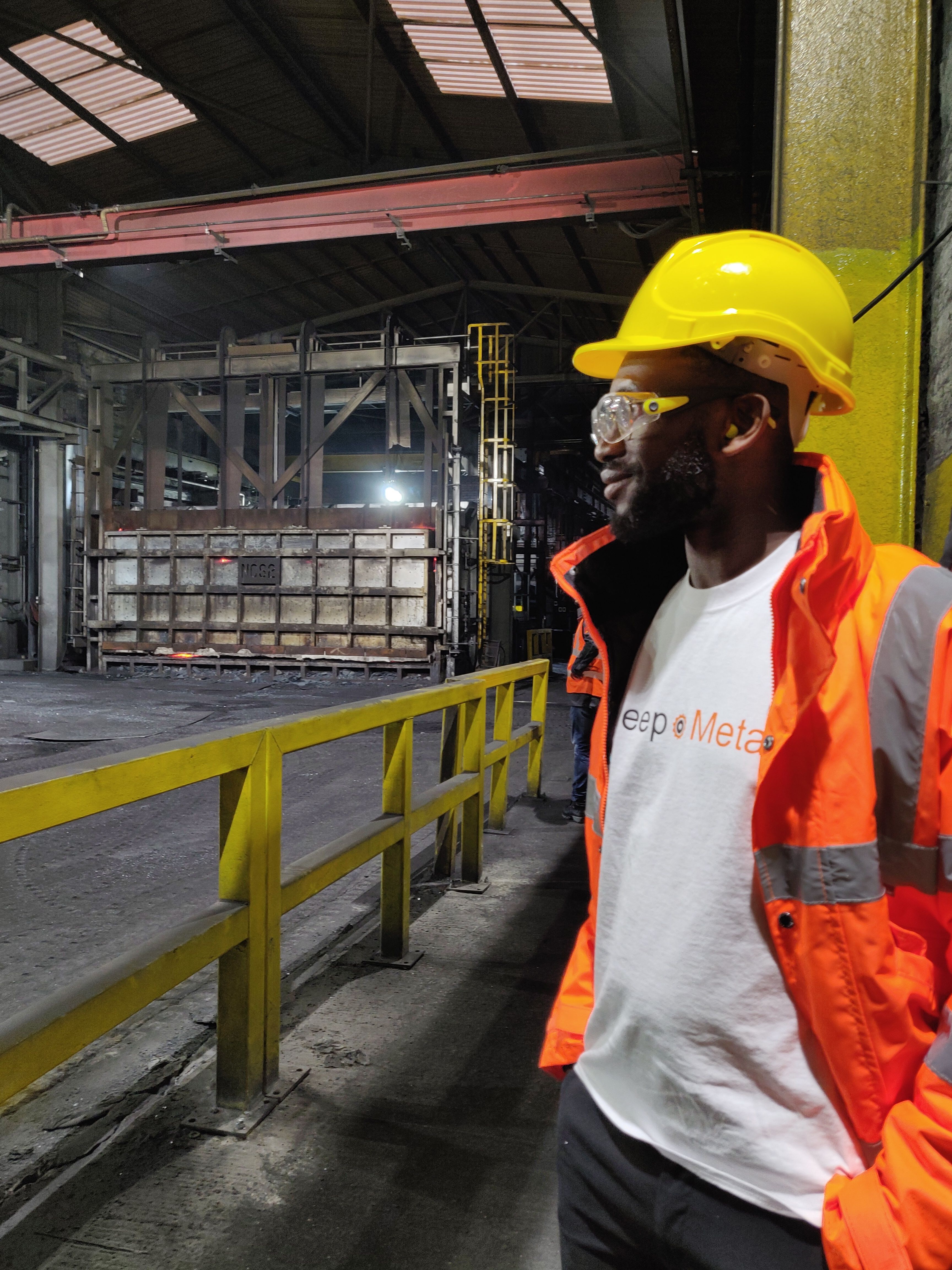
Photocentric
Photocentric develops groundbreaking scalable and sustainable 3D printing innovation
A pioneering 3D printing innovation is transforming mass production, enabling a faster, scalable and more sustainable approach to manufacturing.
Peterborough-based Photocentric led a consortium of industry partners, including Games Workshop, Essentra Components and Unipart, as part of the Made Smarter Innovation Sustainable Smart Factory programme. The project developed JENI, a fully autonomous 3D printing production line that integrates Photocentric’s patented LCD-based technology to produce millions of parts with minimal human intervention.
JENI delivers unparalleled efficiency, manufacturing one platform of parts every 20 seconds – equating to up to two tonnes of components daily. This solution offers up to an 86% reduction in CO2 emissions compared to injection moulding the same parts. If widely adopted, this approach could significantly cut manufacturing emissions while enabling more localised, on-demand production.
While 3D printing offers advantages such as mass customisation and reduced waste, its scalability has been a longstanding challenge. Photocentric’s LCD-based process, which encodes entire print layers at once, provided the breakthrough needed to automate and scale up production.
"This project shows how a single technology breakthrough can support manufacturing sectors as diverse as automotive components and leisure products."
The project built on the company’s pandemic-era success in manufacturing 4 million face shields, demonstrating the speed and sustainability of its approach. Through the LEAD (Low Energy Autonomous Digital) Factory project, Photocentric developed an automated system capable of producing diverse components, from automotive parts to dental aligners.
JENI incorporates advanced robotics to autonomously manage the entire production process, including printing, washing and curing. The system integrates seamlessly with Manufacturing Execution Systems (MES) and Enterprise Resource Planning (ERP) platforms, providing real-time tracking of materials and energy use.
Authentise provided AI-driven nesting and slicing technology, while the Manufacturing Technology Centre (MTC) developed a carbon footprint analysis toolkit to measure the system’s sustainability impact.
JENI’s ability to manufacture parts rapidly without re-tooling makes it a viable alternative to injection moulding, reducing downtime and enabling rapid design iteration. MTC testing validated an 86% CO2 emissions reduction for a plastic PCB clip, highlighting its potential for widespread emissions savings.
The technology also supports localised production, reducing reliance on overseas manufacturing and minimising the environmental impact of logistics. Additionally, Photocentric’s in-house team has developed plant-based materials and recycling solutions to enhance sustainability further.
Building on this success, Photocentric is now exploring AI and machine learning applications to optimise JENI’s automation, efficiency and throughput.
Paul Holt, CEO of Photocentric, said: “This project has been a thrilling demonstration of collaboration to achieve innovation. We have made a giant leap by automating a previously manual process, enabling scale which didn’t exist and driving forward the green agenda with a more sustainable approach to mass production.”
Chris Needham, Innovation Lead for Made Smarter Innovation, said: “This project shows how a single technology breakthrough can support manufacturing sectors as diverse as automotive components and leisure products – and can serve as an inspiration to others regarding how digitally driven solutions could benefit their sector.”
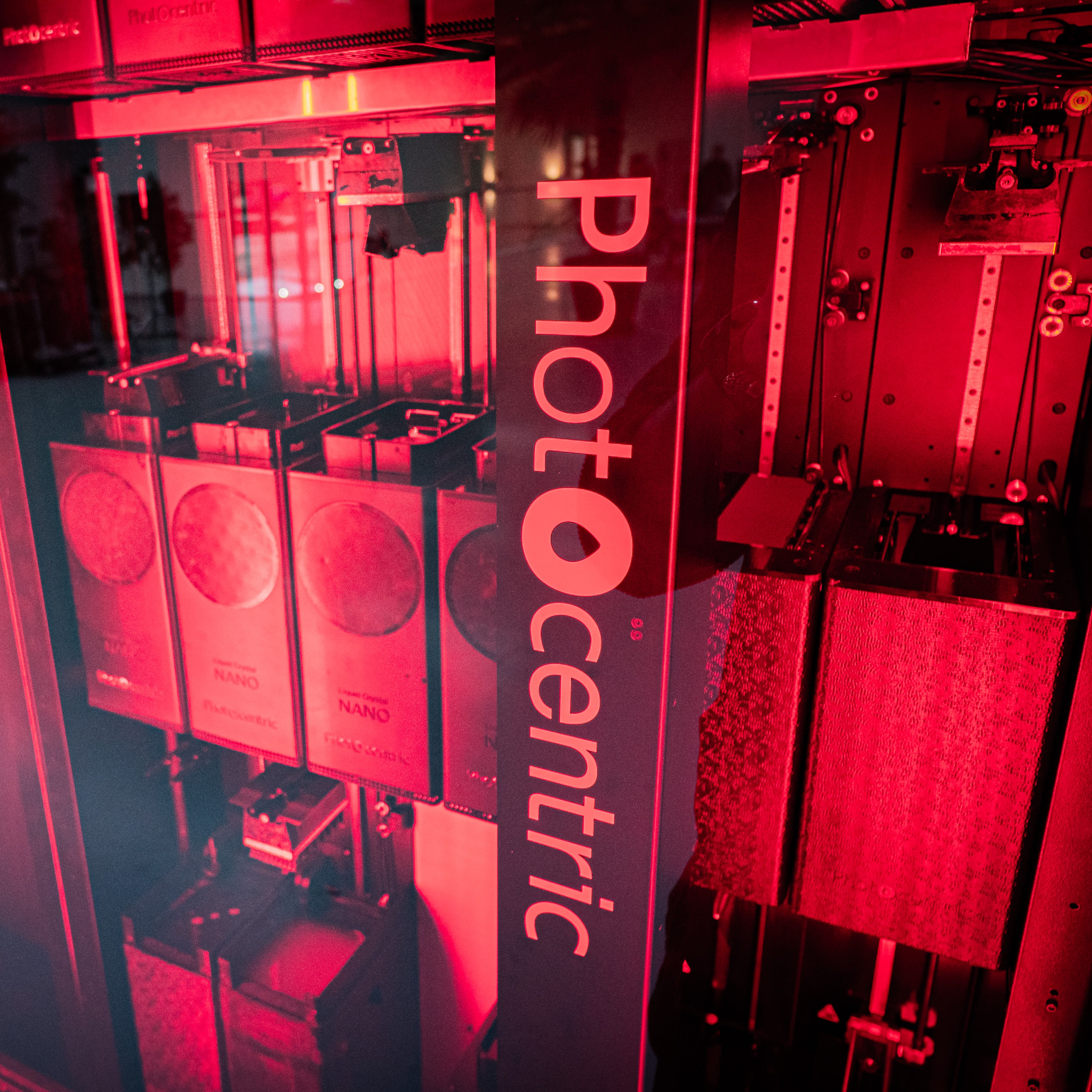
Devtank
This company's innovative smart monitoring solution transforms SME manufacturers through data-led insights
Devtank, a Derby-based smart monitoring specialist, is accelerating digital transformation in SME manufacturing with its innovative IoT solution, OpenSmartMonitor. Supported by Made Smarter Innovation’s Smart Manufacturing Data Hub (SMDH), the device provides real-time environmental and energy insights to optimise efficiency and sustainability.
Through the SMDH’s Lighthouse Project, Devtank has deployed OpenSmartMonitor to 50 UK manufacturers, integrating live data with the Manufacturing Data Exchange Platform (MDEP). This mutual data-sharing approach enables anonymised analytics, unlocking new opportunities for productivity and energy management.
Despite the potential of digitalisation, SMEs often face barriers such as technical knowledge gaps and limited resources. Devtank aims to bridge this divide by offering a low-cost, scalable solution to help businesses monitor energy use, reduce emissions and improve operational efficiency.
Tim Telford, CEO and co-founder of Devtank, said: "Larger firms have embraced Industry 4.0, but SMEs are struggling to keep pace. We want to overcome that by offering SMEs low-cost solutions for energy management and environmental performance to identify efficiency and productivity opportunities."
"Accessing a low cost, flexible open-source method of data capture and analysis is game-changing for SMEs, the sector and the UK’s Net Zero ambitions.”
OpenSmartMonitor features modular sensors that measure environmental factors such as air quality, temperature, humidity and noise, as well as electricity, gas and water consumption. Connectivity options include LoRaWAN, wifi, Power-over-Ethernet, and 4G/LTE, allowing seamless integration into diverse manufacturing environments.
The project has also enabled Devtank to develop its Sustainable Business Intelligence (SBI) model, offering SME manufacturers an ‘out-of-the-box’ digital dashboard to instantly visualise real-time data.
Since launching, Devtank has installed 300 sensors across 50 SMEs, providing critical insights that drive efficiency, including:
- a steel fabrication business that used OpenSmartMonitor to address machine downtime, boosting productivity by 10%
- a door manufacturer that reduced energy consumption while improving material storage conditions
- Ritchie Precision, a precision engineering firm, that is leveraging the technology to monitor energy use and environmental factors for cost savings and sustainability gains.
Hayley Potter, Quality Engineer at Ritchie Precision, said: “Visualising the data from our manufacturing processes has opened our eyes to the opportunity we have to introduce efficiencies into every aspect of what we do. The more data we gather the better our insights will get.”
The project’s success has enabled Devtank to expand its workforce and secure international partnerships, including a reseller in Germany and potential collaboration in Singapore.
Tim Telford said: “There are thousands of SMEs out there that need and want this technology to improve their business performance through resource efficiency analysis. Accessing a low cost, flexible open-source method of data capture and analysis is game-changing for them, the sector and the UK’s Net Zero ambitions.”
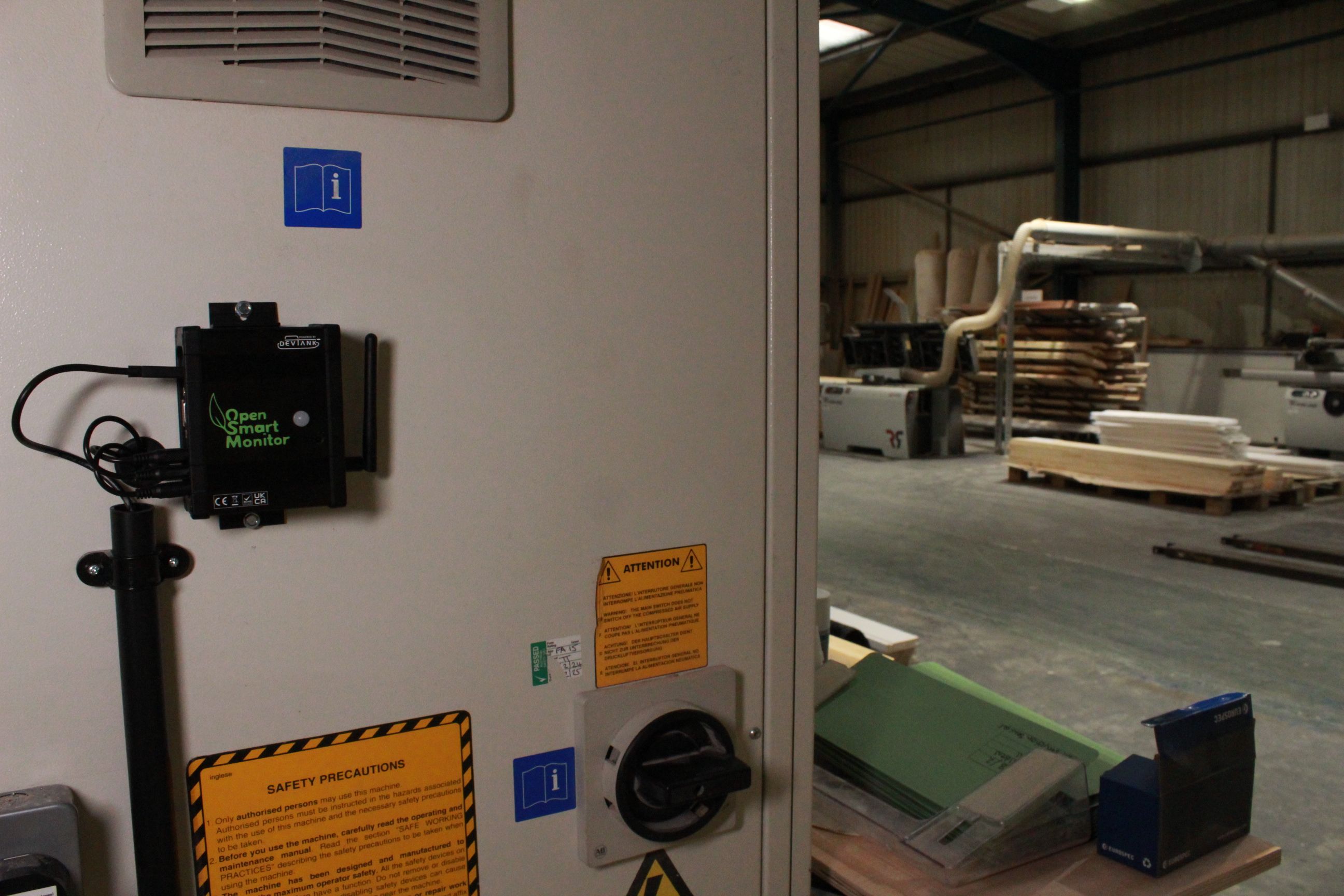
Ryobi
Aluminium components manufacturer unlocks game-changing emissions and efficiencies through innovative energy data project
Ryobi Aluminium Casting, a leading manufacturer of aluminium components, has harnessed the power of data analytics and visualisation to reduce emissions, improve productivity and increase profitability.
The Carrickfergus-based business partnered with Made Smarter Innovation’s Smart Manufacturing Data Hub (SMDH) to integrate a cloud-based platform that enables advanced factory and energy data analysis. Ryobi also contributes to the Manufacturing Data Exchange Platform (MDEP), a data-sharing initiative that allows anonymised insights to be shared across the wider manufacturing ecosystem.
Ryobi produces aluminium components for major automotive manufacturers, including Volkswagen and Jaguar Land Rover, using high-pressure diecasting – an energy-intensive process.
Despite being ISO 14001 certified and equipped with submeters to monitor production equipment energy use, Ryobi lacked a system for analysing and visualising this data effectively. To meet its carbon neutrality goal by 2050, Ryobi recognised the need for a modern, user-friendly platform to extract actionable insights from its operational data.
"Our factories generate vast amounts of data with the potential to unlock efficiency, cost savings and innovation."
Ciarán Maxwell, Low Carbon Project Lead at Ryobi, said: "Our factories generate vast amounts of data with the potential to unlock efficiency, cost savings and innovation. [But to achieve this] we needed a one stop shop for all our data, a modern, bespoke digital tool where we could visualise the opportunities to be more efficient, profitable and environmentally responsible.”
Through its collaboration with SMDH, Manufacturing NI and the Energy Systems Catapult, Ryobi developed a custom digital dashboard integrating:
- electricity sub-meter data from two diecast machines
- production output and Overall Equipment Effectiveness (OEE) data
- granular energy tariff data for cost-impact analysis.
This allowed comparative performance analysis between machines over a three-month period, identifying inefficiencies and opportunities for cost savings.
The dashboard also featured a day-to-day comparison tool, enabling Ryobi to pinpoint variations in energy consumption and determine root causes of inefficiencies.
Early analysis of the data has already delivered significant findings:
- One die-casting machine was found to be 13% more energy efficient and had 11% higher OEE compared to another. Addressing this discrepancy could unlock substantial cost savings and emission reductions.
- The prototype dashboard provided Ryobi with a benchmark for production and energy consumption, paving the way for a fully automated data exchange and real-time visualisation platform.
- Future expansion to all 22 of Ryobi’s diecasting machines could enable smarter production scheduling, cost-competitive pricing and reduced environmental impact.
Building on the success of this project, Ryobi plans to implement a new real-time database to further automate energy monitoring and process optimisation.
“Once the platform is up and running we are expecting to reduce our overall energy consumption by up to 20% in the first year,” Ciarán said. “For an energy intensive business like ours, that would be huge. It will unlock capital to invest in renewable technologies and chase reduced energy consumption and spend further.”
By embracing digital transformation, Ryobi is setting a new benchmark for energy-efficient, data-driven manufacturing in the UK.
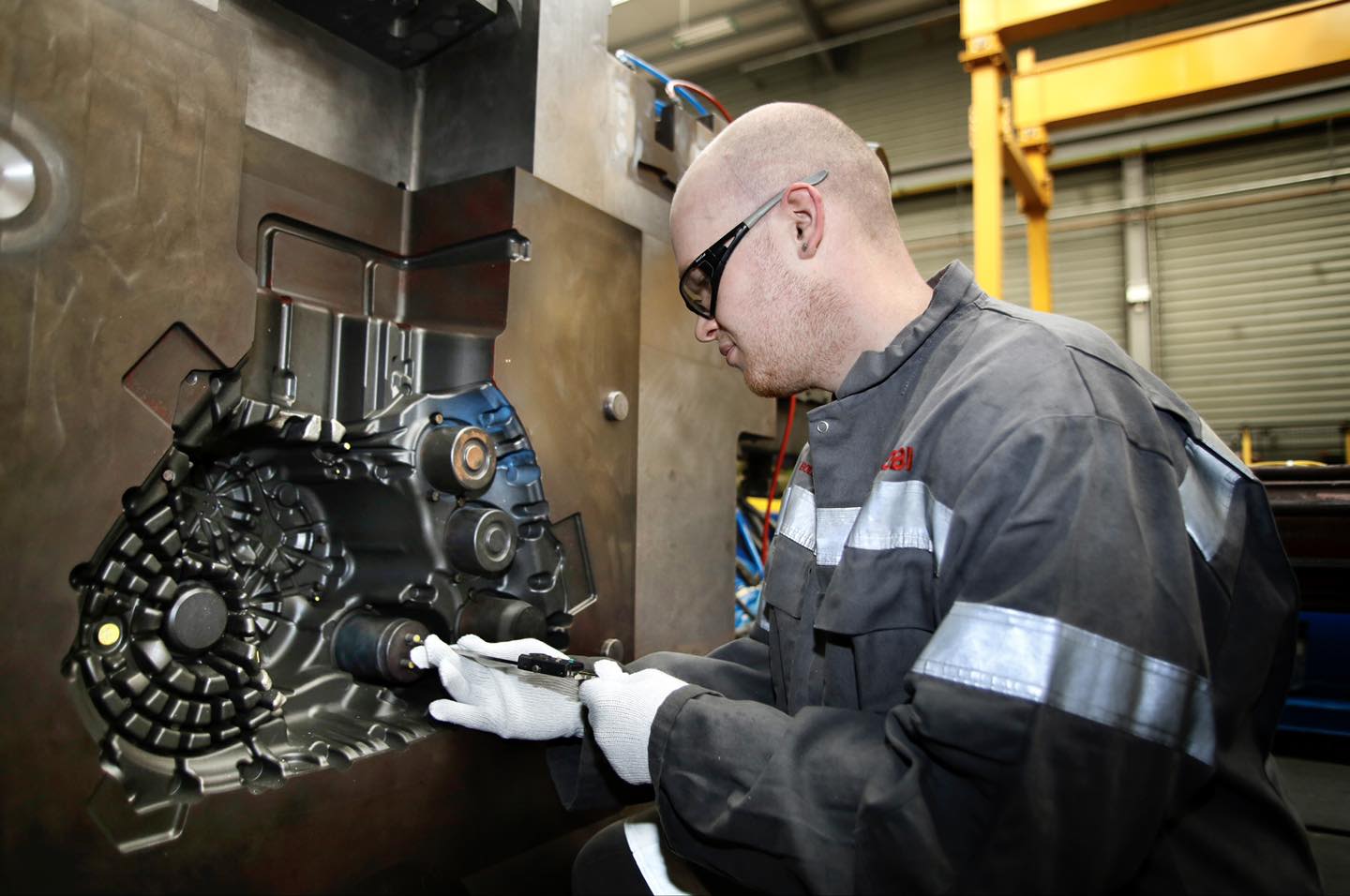